Production Engineer
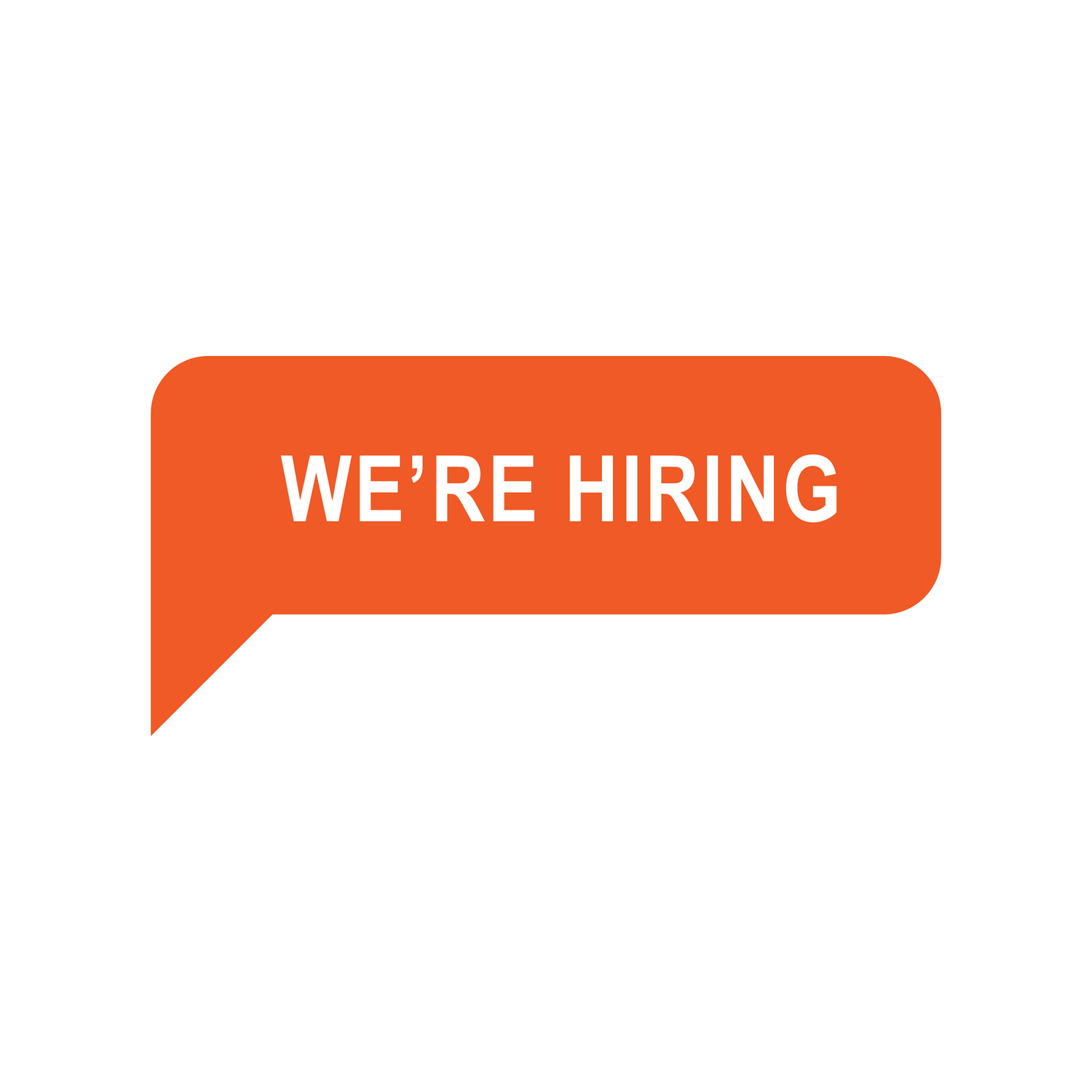
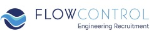
Confidential
2021-12-03 08:59:40
Manchester,
Lancashire,
United Kingdom
Job type: fulltime
Job industry: Engineering
Job description
Our client, a leader in the valves and rotating equipment industry, is looking for an experienced production engineer to join their growing team in the Greater Manchester region. Find details of the role below:
Responsibilities/Duties
1.
To drive the introduction of new products and prototypes, arrange manufacture of samples, carry out design and arrange manufacture of jigs, fixtures, test rigs and production line workflow, assist with product testing/evaluation at the type test stage, assist with 'O' series batch runs & assist with supply chain setup of new products.
2.
Developing manufacturing methods and deliver new products into production.
3.
Challenge the 'norm' and deliver continuous improvement, operational excellence and LEAN improvements incl introduction of alternative manufacturing techniques, layout changes & automation.
4.
To work on lean initiatives in the business in order to remove waste from all processes.
5.
Assist with the introduction of new equipment, processes and projects into the facility
6.
Develop processes and technology to improve the products in terms of quality and cost.
7.
To help re-engineer cost out of the products from within internal processes/product design and externally through the supply chain.
8.
To have the responsibility for all the products manufactured at the site with respect to:
o Local project management for the client of new products being introduced in accordance with company PRF/PCF system including due consideration of interfacing with applicable OEMS (e.g. Rotork actuators, gearboxes).
o Produce work instructions for the production operatives for all company manufactured products.
o Technical support on company products (internally and externally).
o Assist QA with root cause analysis of customer complaints which may necessitate site visits, (co-ordinated with Technical Manager - Water), and recommend corrective and preventative action to prevent re-occurrence.
o Monitor national standards/specifications with representation on committees if applicable, (co-ordinated with Technical Manager - Water).
o Participate in innovation days with customers to highlight new products/ improvements, (co-ordinated with Technical Manager - Water).
o Technical training of both manufacturing and sales personnel to cover the technical aspects of the product including benchmarking of company products vs the competition, (co-ordinated with Technical Manager - Water).
o Supply technical data for the client for all marketing data (data sheets, O&Ms, Presentations, Brochures, etc.).
1.
To assist in quick turnaround of item cards, BOMs, drawings for product variants (POF) based on existing product offer for manufacturing.
2.
To support the QA department, if and when required, with sample authorisation and NCR's.
3.
To manage and monitor Technical Master Data in line with the company Logical Number System including items, descriptions, BOMs, drawings, data sheets and operating and maintenance instructions.
12.To carry out critical competitor product evaluation compared to the client's offer considering National standard and specification requirements.
13. Ensure you show regard for your fellow colleagues.
14. Ensure all company procedures are followed at all times.
15. Ensure health and safety regulations are adhered to at all times.
The above is not an exhaustive list of duties and you will be expected to perform different tasks as necessitated by your changing role within the organisation and the overall business objectives of the organisation