Production Supervisor -Team Lead
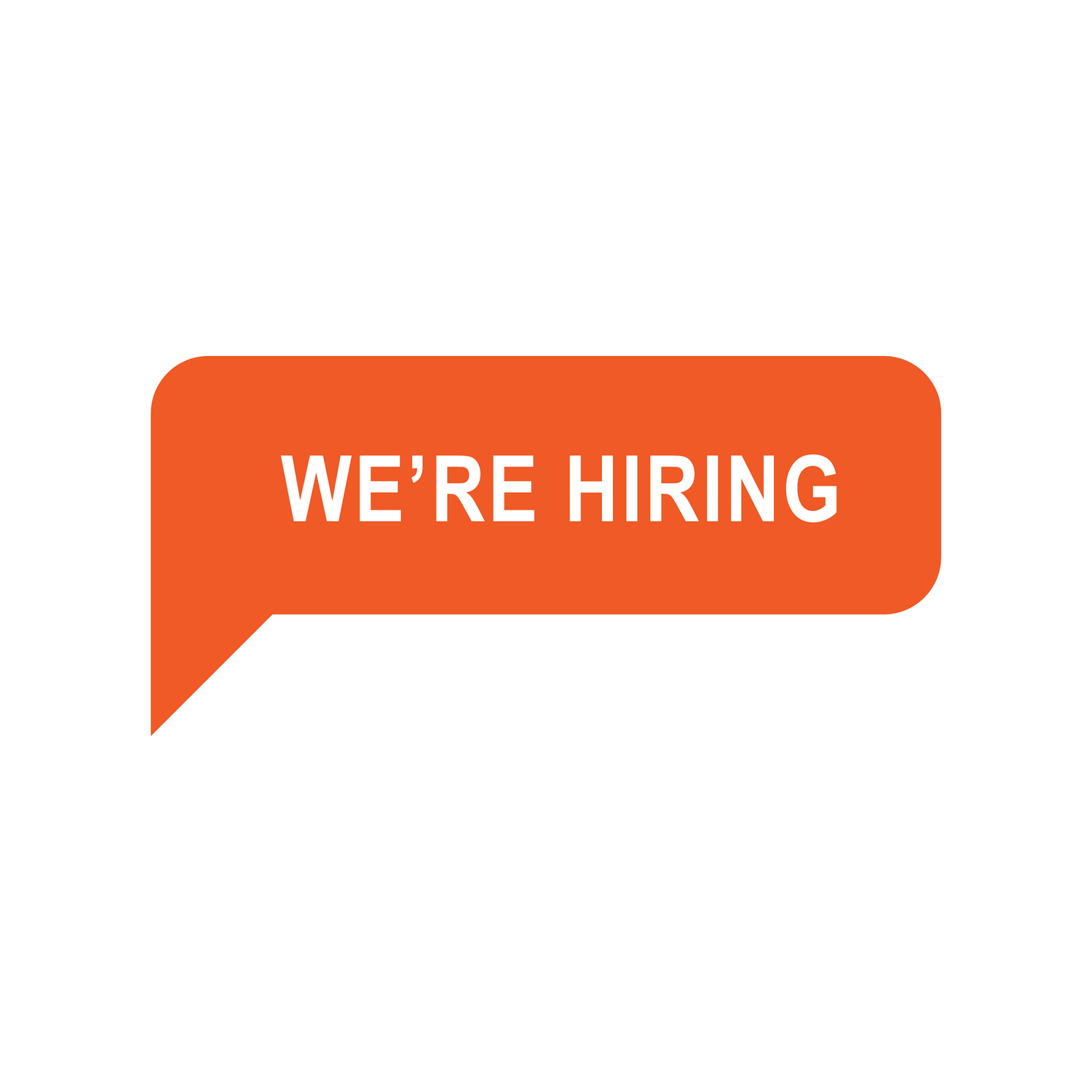
Bonduelle Fresh Americas
2021-12-04 01:00:03
Acton,
California,
United States
Job type: fulltime
Job industry: Manufacturing Operations
Job description
What if your job had a real impact? Join us at Bonduelle to start an adventure where people come first and contribute to a better future through plant-based food! By joining Bonduelle, the world leader in ready-to-use plant-based food, you are deciding to make a positive and sustainable impact on yourself, the others and the planet. You will play an active part in our mission: "inspire the transition toward a plant-based diet to contribute to people's well-being and planet health". Bonduelle is a family-run company of 14,600 people which provides over 100 countries with vegetables.
As Production Team Leader, you will be responsible for supervising production associates on your assigned shift in order to drive a safe and highly efficient production operation to produce high-quality fresh food products. This position requires strong leadership skills; people and process development are critical in this role. The Production Team Leader must mentor frontline coordinators and associates, and contribute to continuous process improvement, and ensure that proper quality, sanitation and safety guidelines are being met. In addition and depending upon the assigned shift start time, Team Leads will be responsible for start-up, pre-production procedures prior to the beginning production for the day. What you will Do:
- Ensure the safety of all employees in the operation of equipment through proper training, enforcement of safety rules, documentation, and following proper procedures and GMP protocols.
- Oversee pre-production, start-up procedures (1st shift every work day; 2nd shift on Sunday and Monday) including following set guidelines to prepare production lines, removing condensation/water, starting automated equipment/machines, meeting strict timelines and ensuring the lines are ready to operate by the time production staff arrives
- Produce and package a high-quality product using proper procedures and adherence to good manufacturing practices and government standards in cooperation with the Quality & Food Safety department. Responsible for reporting and taking action on food safety and quality problems to the appropriate personnel, as well as following quality and safety programs and policies themselves in order to ensure products made meet the highest standards possible.
- Ensure production lines are operating efficiently and running at targeted throughput. Complete hourly audits for safety, quality, cost, and line performance. Develop and execute action plans to address any gaps in efficiencies.
- Drive continuous improvement initiatives to ensure that downtime is minimized, and yield is maximized. Execute action plans to ensure root causes of unplanned downtime are addressed.
- Manage Production Schedules and employee schedules and ensure correct crewing and de-crewing processes are being followed in accordance with crewing standards.
- Build people capability through effective employee relations, hiring, training and communications for frontline hourly associates. Coach and mentor frontline workforce to drive line productivity, efficiencies and yields.
What you will Need:
- Bachelor's degree preferred
- Minimum of 2 years supervisory experience in a fast-paced production environment or other equivalent experience.
- Strong verbal and written communication skills. Bilingual skills are highly preferred.
- Ability to work a flexible schedule.
- Ability to work in a cold environment (70% of time in 34°F, 30% administrative office work).
- Demonstrated ability to work in a team-based fast-paced, changing work environment.
- An understanding of production procedures, safety processes and food safety/quality requirements is desired (FDA compliance).
EOE/AA/M/F/Vets/Disabled