Quality Assurance Manager
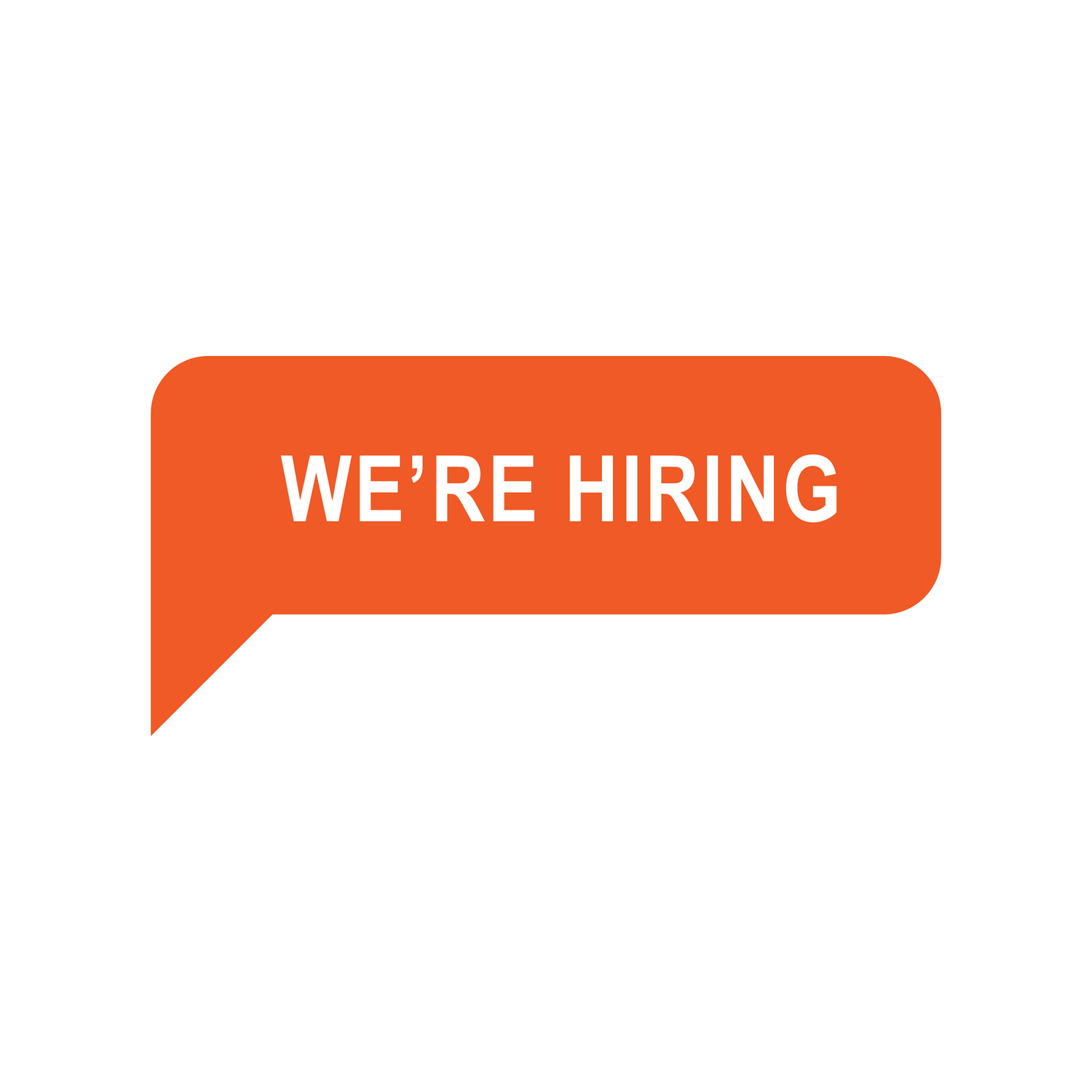
TELEIOS VII, LLC
2021-12-04 07:30:03
Azusa,
California,
United States
Job type: fulltime
Job industry: HR / Recruitment
Job description
SUMMARY STATEMENT
Quality Assurance Manager is responsible for leading the development, implementation, and administration of the Quality Program and Quality System Plan (including SQF System, HACCP, Food Safety, GMPs, Allergen Control, Chemical Control, Traceability, Nonconforming Procedures, Government and Customer Requirements, etc.). An important part of this is leading the investigation and communication of quality-related issues and the subsequent corrective/preventive actions. The Quality Assurance Manager will be fully functional in all areas of food safety to give direction in any area needed in the plant.
GENERAL RESPONSIBILITIES
1.1 Develop the Quality Assurance department goals and obligations and ensure they are met. This includes completion of testing, investigations, and reporting in a timely and effective manner.
1.2 Provide supervision, training, and development of QA Supervisors, Leads, Technicians, and Sanitation team. Lead the training of other departments regarding Quality programs and issues.
1.3 Provide information and develop or share tools for personnel to maintain a high standard of attention to quality and for the company to continually improve the effectiveness of its Quality Systems.
1.4 Maintain good communication with other internal functions, outside suppliers, customers, and senior management. Demonstrate the ability to influence and lead change across the organization.
1.5 Serve as the primary liaison and leader for corporate R&D in the factory.
1.6 BRC or SQF, HACCP, PCQI, and Food Defense Certified
ADMINISTRATIVE DUTIES
2.1 Ensure that job responsibilities of QA Supervisors, Leads, Technicians, and Sanitation team are understood and applied. Manage job performance based on these responsibilities.
2.2 Schedule, organize and hire QA Supervisors, Leads, Technicians, and Sanitation team as determined by production schedule, management directions, and department needs.
2.3 Review and sign all QA documentation.
2.4 Verify timesheets and approve overtime, sick days, vacation, absences, and tardiness for the QA department.
2.5 Represent QA in all regular interdepartmental and corporate meetings.
2.6 Validate and sign off on changes made to product labels and specifications.
ANALYTICAL RESPONSIBILITIES
3.1 Establish retain policy and process and ensure it is being executed correctly.
3.2 Verify and validate Sensory Program and utilize results to drive decisions.
3.3 Monitor the equipment calibration status and certification of all measuring and testing devices in the facility and see that they are renewed as required.
3.4 Establish environmental testing program, execute, and evaluate the results.
3.5 Maintain ingredient and packaging material documentation including current Specifications, MSDS, Nutritional Data, Letters of Guarantee, etc. as required.
3.6 Monitor the traceability of ingredients, packaging materials, in-process items, and finished products. Conduct regular mock recalls testing the effectiveness of the program.
3.7 Facilitate successful audits by third parties and regulatory agencies.
3.7.1 Provide and submit documents, forms, etc. to the auditing agency as requested.
3.7.2 Investigate the company's readiness for the audit and report or correct deficiencies that are discovered.
3.7.3 Maintain records of Audit reports and comply with requests for corrective actions and follow-up communications.
3.8 Responsibility and authority to oversee the SQF System.
3.9 SQF Practitioner for Validation and Verification of SQF Pre-requisite programs.
3.10 Accountable for the safe and wholesome manufacture of our food products.