Mgr Operational Excellence/Continuous Improvement
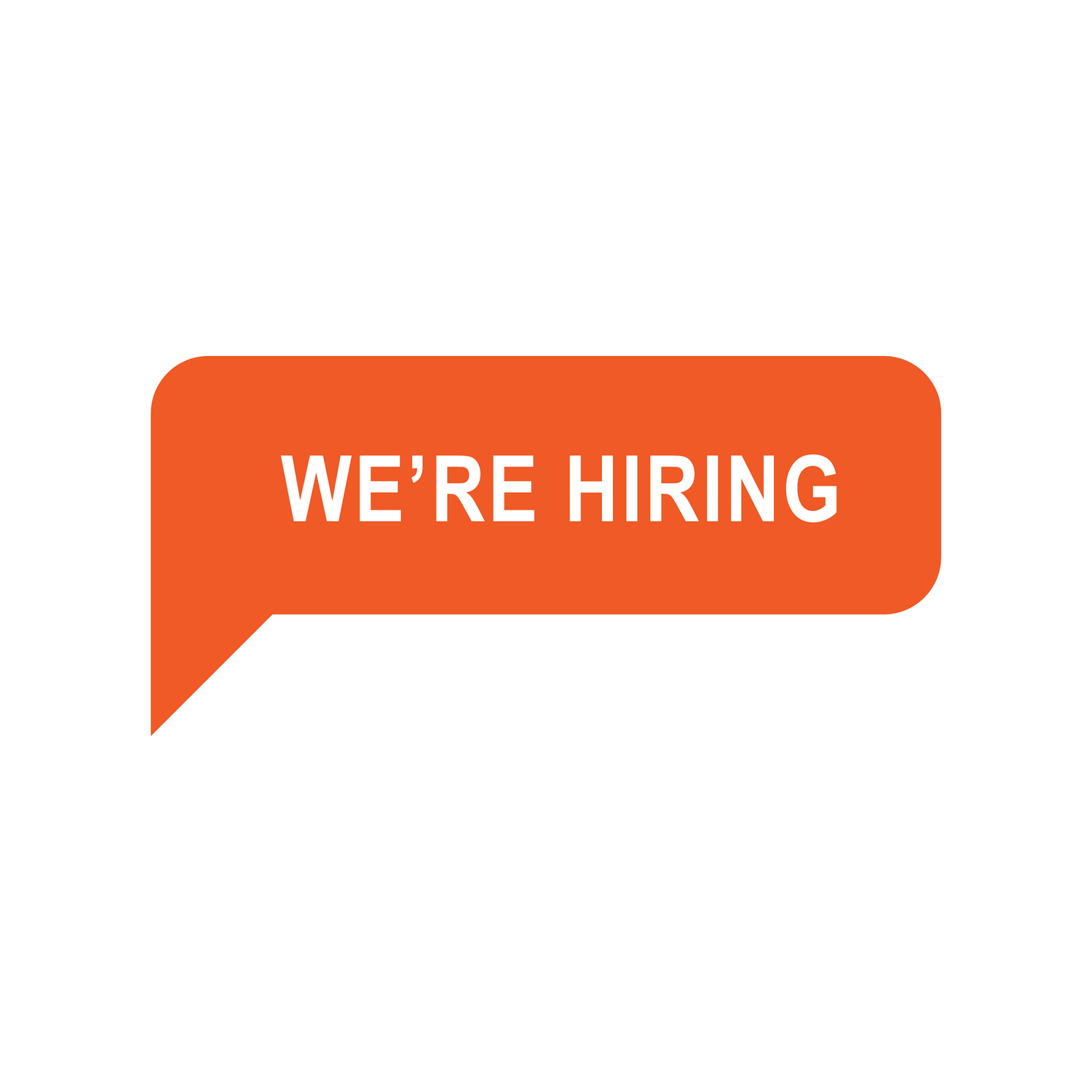
General Dynamics Ordnance & Tactical Systems
2021-12-03 13:00:03
San Diego,
California,
United States
Job type: fulltime
Job industry: Consulting & Corporate Strategy
Job description
Overview:
This position will have responsibility for process optimization and continuous improvement through the implementation of Lean Manufacturing on the shop floor. The position will catalogue and manage a database of improvement projects. This includes supporting the day-to-day operations of the manufacturing processes and monitoring progress of process improvement, resource identification and allocation. This position reports to the Director, Operations and is responsible for the leadership and oversight of the company's continuous improvement systems.
Major Position Responsibilities:
Essential Duties and Responsibilities: Include the following. Other duties may be assigned.
Coordinates and promotes CI activity within Operations, Engineering, and Quality
Supports plant production of existing product lines with a focus on eliminating defects and waste while identifying and implementing best Lean practices focused on improving processes
Sets Goals driven from KPIs for executing Lean manufacturing business benefits (quality, cost reduction, efficiency improvements, manufacturing value enhancement, data integrity, Value Stream Mapping) that ensures transparency of delivered benefits to the facility.
Use of Lean Manufacturing, Toyota Production System and project management tools and practices, as well as Lean capabilities to prioritize activities, drive a structured business improvement program and ensure that the team members put in practice a project management way of thinking and it becomes embedded in the culture (PDCA, DMAIC, responsibilities and accountabilities, project review discipline, Problem Solving Discipline).
Coordinates the enhancement and enforcement of standard operating processes for all operations within the business
Consolidates Continuous Improvement processes and ideas where possible and streamlines them towards one joint goal
Develop and implement a strategy for fostering and improving the lean and project management capabilities and behaviors of employees, Managers and Supervisors. This includes coaching, training and driving the tools and capabilities in place to get plant-wide results for management of projects and initiatives.
Provides multiple levels of training for all department team members: lean training, quality training, team building, cross training, etc., assisting each team member in growing individually in preparation for further advancement
Interacts with the Plant Leadership Team in developing strategic vision and action plans, ensuring the quality management system is implemented, functioning effectively and continuously improved through coordination with Operations
Assists Operations in the training of operators on new procedures, oversee all projects campus wide, assuring that they are meeting objectives and projected savings
Facilitates individuals or teams through a formal problem solving methodology and develops a prioritizing system for problem solving initiatives
Facilitates interpretations of the budget and impacts of the counter-measures and verify savings accomplished and align them with target costing and divisional initiatives
Job Dimensions (Budget, Staff, Work Environment, etc.):
Responsibility for process optimization and improvements, participating in the acquiring and installation of new technologies and implementing cellular manufacturing technology (Flow Manufacturing) and or managing a vast database of improvement projects. This includes supporting the day-to-day operations of the manufacturing processes and monitoring progress of process improvement, resource identification and allocation.
Physical Demands:
The physical demands described here are representative of those that must be met by an employee to successfully perform the essential functions of this job. Reasonable accommodations may be made to enable individuals with disabilities to perform the essential functions. Often required to sit, repetitive hand motion (such as typing), hear, listen, talk, stand, walk and lift - up to 10 pounds. Seldom required to bend, stoop, climb stairs, climb ladders, kneel, squat, crouch, balance, and reach overhead, pull, push or lift - up to 50 pounds.
Basic Qualifications:
Major Competencies/Skills:
Communicate Transparently
Lead the Team
Impact and Influence
Deliver Results
Coach and Develop
Lean Manufacturing / Toyota Production System
Education and/or Experience:
Bachelor's degree in Business, Engineering, Operations or related field with 6-8 years of relevant experience or equivalent
3-5 years of Supervisory/Leadership experience
Knowledge of advanced quality tools like FMEA, DOE, QFD, 6-sigma
Basic knowledge of COQ (cost of quality) and how it relates to problem solving
Understanding of quality management systems ISO9000/AS9100-RevD
Bi-lingual (English/Spanish) required
5% Travel Required