Materials Manager
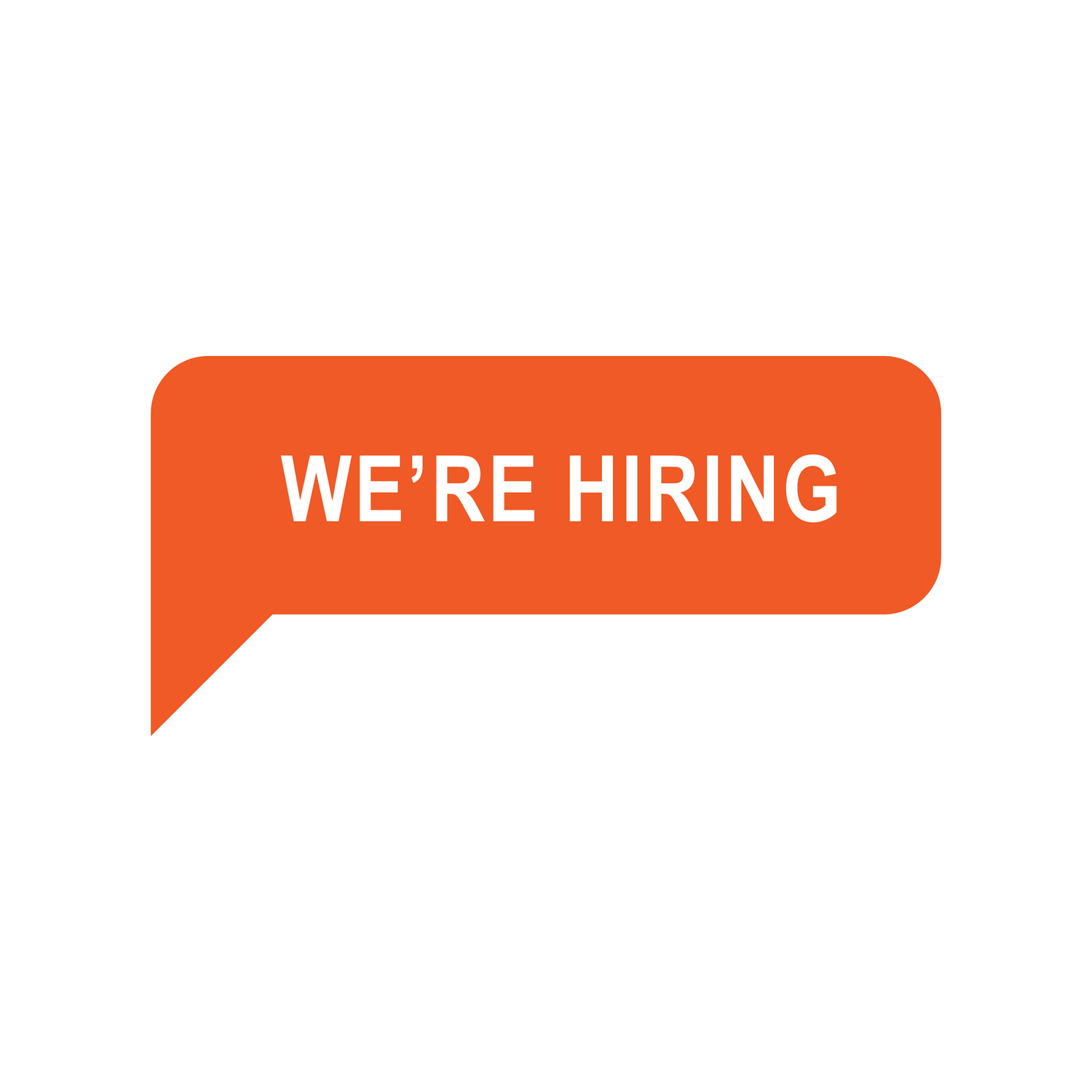
International Medical Industries
2021-12-03 17:31:37
Pompano Beach,
Florida,
United States
Job type: fulltime
Job industry: Retail & Consumer Products
Job description
JOB TITLE: Manager, Materials
DEPARTMENT: Operations
REPORTS TO: Vice president, Operations
GENERAL STATEMENT OF DUTIES:
The Materials Manager provides direct management of materials personnel related to the materials and Production Control aspects of IMI.
The primary role of the Material Manager is to plan, organize and control the shipping and receiving warehouses and production to meet Sales requirements, while maintaining acceptable finished goods inventory levels, this includes on-time delivery in required quantities to satisfy customer demand.
TRAINING: Each member of management is responsible for maintaining current and accurate Training Matrices for all direct report employees. Further, they are responsible for timely execution of their employees' required training and to assure that a documented verification of effectiveness of that training has been performed and recorded. And finally, they are responsible to assure that no job task is performed by their employees until current training is complete, verified, and recorded.
ESSENTIAL DUTIES AND RESPONSIBILITIES:
- Develop, implement, and manage a planning process that incorporates make versus buy, capacity planning and scheduling, finished goods inventory, and cost elements to optimize inventory.
- Performs analysis of customer demand, sales, and historical material usage to develop and execute build to order and build to forecast plans.
- Provide monthly inventory variance analysis in conjunction with executive management requirements. This would include aging of inventory on hand.
- Implements and manages an inventory control system capable of identifying discrepancies in inventory counts and taking corrective action to guard against inconsistencies in the future.
- Collaborates with cross-functional business teams to develop the best economic strategy for production planning to support customer demand.
- Implements and manages a finished goods inventory control system capable of identifying discrepancies in inventory counts and taking corrective action to guard against inconsistencies in the future.
- Identifies, coordinates and reviews cost accounting projects, such as pricing and margin analysis, customer, market and product profitability, data warehouse integrity and reporting, etc.
- Manage the distribution and logistics functions including shipping, receiving, warehouse operations, and freight.
- Prepares and maintains warehouse and planning department budget and expenditures.
- Maintain a safe and healthy work environment by implementing, maintaining, and aligning company polices that adhere to local, state, and federal environmental, health and safety regulations.
- Manage employee talent and development. Coordinate performance reviews, recruitment/hiring, technical training, salary adjustments, corrective actions, and employee relations. Maintain results through coaching, counseling of staff and setting meaningful and measurable goals. Provide growth, training, and development opportunities to employees.
SUPERVISORY RESPONSIBILITIES:
- Manages the planning team to develop and report on schedules for Sales and shipping activities.
- Ensures operational production requirements are met by reviewing the scheduling and assigning of employees, following up and reviewing results with personnel,
- Recruit and select new employees, ensure that the orienting and training schedule for new employees is followed and documented, review progress reports for new employees.
- Maintains materials operational results by coaching and counseling front line employees; Monitoring and appraising overall performance; ensure that the coaching and counseling sessions of all employees is documented.
REQUIRED
1.Bachelor's degree in Materials, Supply Chain, Accounting, Math, Business Administration or related field required.
2.Ten (10) years production planning, purchasing, inventory, production scheduling and control, logistics or related experience in a manufacturing environment, with exposure to manufacturing business systems and models, BOM management, and purchasing.
3. Five (5) years of supervisory experience.
4.Experience in a complex manufacturing environment.
5.Experience in manufacturing a Medical device .
6.Working knowledge of Material Requirements Planning systems, parameters and theory.
7.Must possess excellent organizational, analytical, interpersonal, communication, and computer skills to include ERP systems.
8.Outstanding leadership, organizational, multitasking and problem-solving skills
9.Proficient computer skills, e.g. MS Word, Excel, electronic inventory & planning
PREFERRED BUT NOT REQUIRED
10.Has developed and trained cGMP/GDP to FDA-oversight companies.
11.Lean Manufacturing/KANBAN
12.Extensive knowledge of the ISO/FDA requirements for medical devices
PHYSICAL DEMANDS:
Physical activity includes walking, standing, bending, squatting, reaching above shoulders and lifting to 40lbs. Must be able to drive an automobile for short and long distances.
WORK ENVIRONMENT:
Performs primarily office activities in a lighted and ventilated area. May be subject to changes in temperature and exposure to dust. Will be exposed to uncontrolled environmental conditions during driving. Will work in a normally acceptable office environment, production floor, or warehouse, with no abnormal hazards or risks. Reasonable accommodations may be made to enable individuals with disabilities to perform the essential functions.
**COVID-19 Vaccine Required**
PI