Lead Quality Engineer
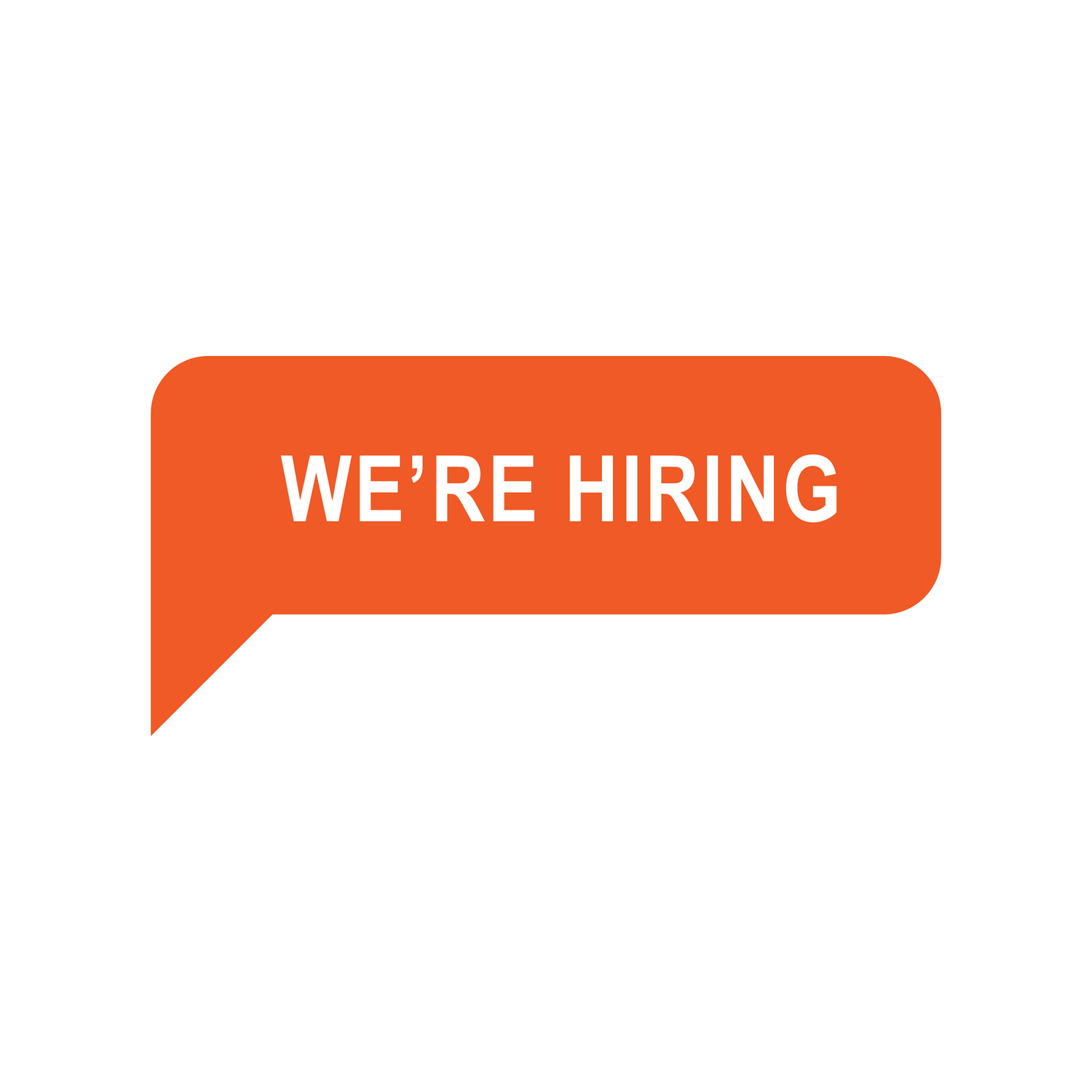
Middle River Aerostructure Systems
2021-12-03 17:31:46
Baltimore,
Maryland,
United States
Job type: fulltime
Job industry: Engineering
Job description
Description:
Middle River Aerostructure Systems is a world-leading manufacturer of thrust reverses (the braking system on a jet engine), engine nacelle components and specialized aerostructures. It supplies and supports these products for engine makers, airplane manufacturers and aircraft operators. Located on Maryland's Chesapeake Bay near Baltimore, MRAS has a 1.7-million sq. ft. facility situated on 180 acres - where the company and its predecessors have designed, built and equipped civil and military aircraft for nearly 90 years. In 2019, MRAS was acquired by VT Systems, the U.S. affiliate of Singapore-based ST Engineering - becoming a part of its global network of aerospace facilities and offices. With the ownership change, the company was renamed Middle River Aerostructure Systems.
Role Summary/Purpose:
The Lead Quality Engineer will have responsibility of all Quality functions for a specific program within the Composite Bonding operations. The individual will be responsible for ensuring all engineering and regulatory requirements are met to meet customer satisfaction and safety. The Lead Quality Engineer will be a part of a cross-functional technical and operations team to focus on achieving the business objectives.
Essential Responsibilities:
· Independently manages all Quality functions of assigned program(s) or area(s)
· Acts as the Point of Contact for their program to inspectors and all supporting functions (Ops, Engineering, Sourcing, etc.)
· Design and develop processes that produce conforming and compliant parts
· Understands AS9100 and NADCAP requirements
· Operates independently to support production by providing concrete direction
· Able to self-prioritize and manage multiple priorities simultaneously that align with business objectives
· Eliminate process variation and product defects through creative solutions
· Drives Root Cause, Corrective Action from start to finish independently using established RCCA tools (PFMEA, DMAIC, Apollo, 5 WHYs, 8D, etc.)
· Determine product and process data to be collected; collect and use appropriate statistical tools to analyze data and recommend process improvements.
· Engaged on all non-conformances, and drives the MRB disposition and lifecycle using signature authority
· Actively leads and participates in lean projects that improve Quality, output, cost, etc.
· Is able to be a lead in technical discussions (acts as a pseudo-project manager between cross-functional teams)
· Is able to take ambiguous direction and create a comprehensive execution plan
· Effectively/professionally interfaces with external customers on a regular basis without guidance
· Makes sound business decisions and is unafraid to challenge the status quo
· Creates and pitches presentations to leadership and customers, when required
Associate's/Bachelor's Degree from an accredited university or college with a minimum of 5 years of experience in a manufacturing or quality leadership role. Bachelor's Degree in appropriate science, engineering, and/or engineering technology field is preferred.
•Composite experience is a plus.
Desired Characteristics:
•Strong oral and written communication skills.
•Strong interpersonal and leadership skills.
•Experience leading and implementing change.
•Experience performing internal audits and participating in external audits.
•Exceptional analytical, problem solving, and root cause analysis skills.
•Ability to multitask and handles tasks with competing priorities effectively.
•Demonstrated knowledge of Quality Management System tools, continuous improvement methodologies and in-depth understanding of site level products and related processes.
•Detail oriented and strong computer skills.
•Experience with ERP software applications and Microsoft Excel/PowerPoint/Word.
•Comprehensive understanding of ISO 9001/AS9100 Quality Management Systems.
•Experience with CATIA, or another 3D modeling software.
•Experience with lean manufacturing and/or 6 Sigma techniques.
•Preferred minimum of 3 years of experience in Production Quality.
PM19
PI