QA Production Supervisor SQF
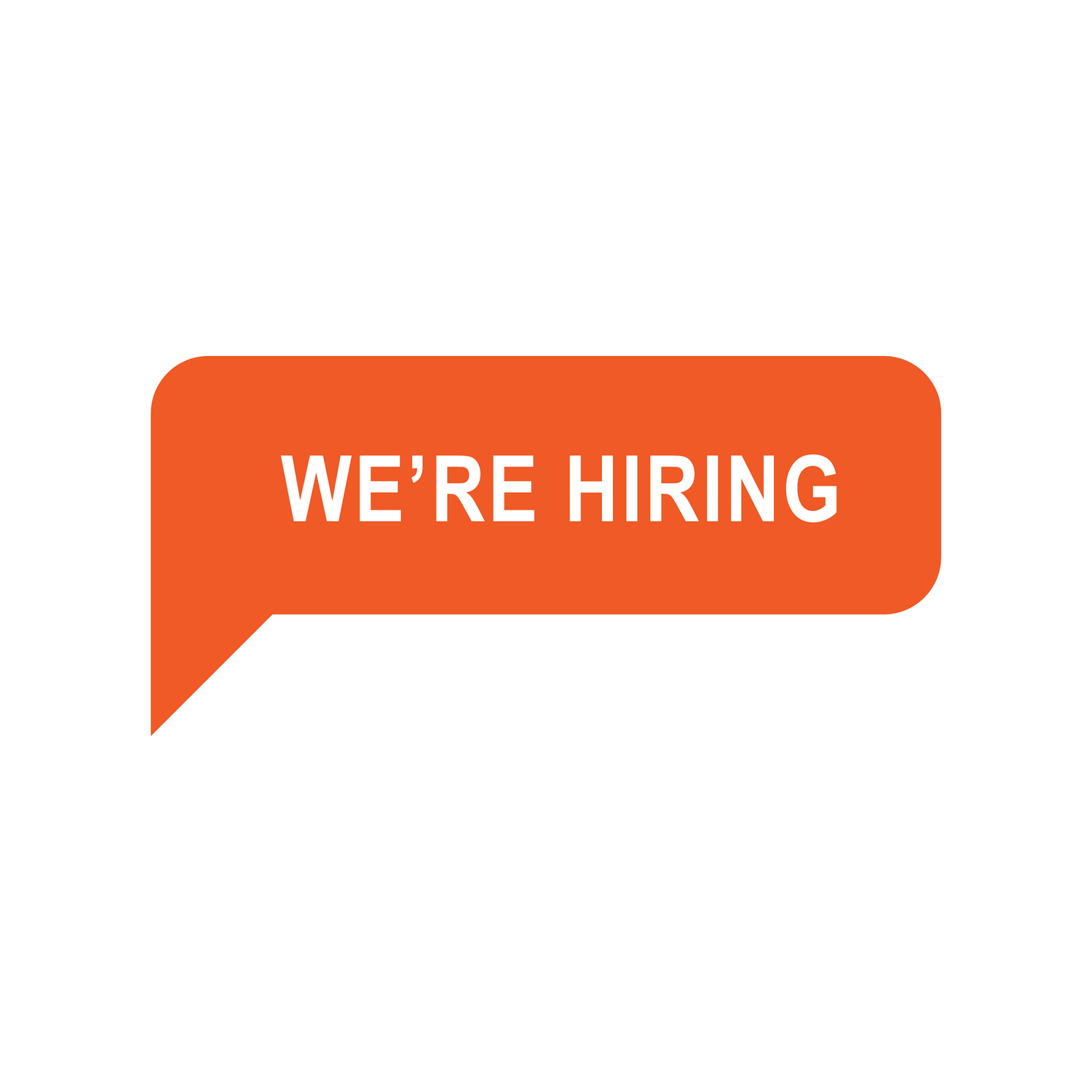
psoc 78000.00 US Dollar . USD Per annum
2021-12-03 12:39:43
Chicopee,
Massachusetts,
United States
Job type: fulltime
Job industry: Manufacturing Operations
Job description
Plastic Manufacturer.
Must possess SQF Certification.
Local Candidates ONLY.(Springfield, MA)
Schedule: Shift: 1st shift
Monday through Friday
7:30 AM 5:00 PM (1/2 hour lunch)
This is an 9-10 hour per day position.
Overtime: This is a salaried position and as such may require schedule modifications to complete the job duties..
POSITION OBJECTIVE:
The Objective of the Quality Assurance Supervisor is to ensure that SQF Policies and Programs carried out with the following results:
• All products meet or exceed customer expectations;
• All products and quality-related processes meet the requirements of the Quality System;
• The Quality System is maintained, updated and improved as needed to ensure its suitability for meeting the needs and continued conformance to the SQF and ISO 9001:2000 quality standards.
RESPONSIBILITIES:
• General
a. Serve as a model Quality Policy in action. Exemplify professional behavior, hard work and commitment to customer satisfaction.
b. Maintain the Quality Lab, the staging area, and mezzanine storage, making sure these areas are clean, ordered and organized.
c. Attend and participate in meetings regarding Quality and SQF matters.
Key Responsibilities:
• Plans, organizes, leads, controls, and coordinates the day-to-day activities of associates involved in providing services in the area of Quality Assurance. Operates with minimal supervision and reports to the Director of Engineering. Works closely with all operational areas of MSA as well as other locations within the business and our client contacts as needed by business.
• Quality Assurance Supervisor will create and assist with developing:
a. Short and long-term goals and plans for quality auditors in conjunction with the Chief Financial Officer.
b. Monitoring requirement goals, monitoring attributes and definitions, and ongoing quality initiatives.
c. Provide internal reject reporting to Chief Financial Officer.
• Quality Assurance Supervisor will present and lead:
a. Calibration sessions with supervisors, management, and training department.
b. Supervise the delivery of refresher trainings and coaching with the training department.
c. Maintain & administer audit system for internal & external products and retain master scorecards.
• Quality Assurance Supervisor will supervise:
a. QA Auditors: coaching, scheduling, training, monitoring performance, and conducting performance reviews.
• Responsibility of working with others:
a. Responsible for the management of Quality Assurance Auditors as they work with Shift Supervisor and team leads. Quality will verify that Shift supervisory personal understand why a rejection occurred and work with them as they re-train their staff. At the request of an individual supervisor or at the instruction of the Director of Engineering, QA supervisor may under take shift training for a particular article or a particular individual. If individual employee instruction related to quality concerns is deemed necessary the QA Supervisor should first address the concern with the Shift Supervisor to agree on who will directly engage an employee for instruction.
• Quality System
a. Serve as the Management Representative for the Quality System as described in section 5.5.2 of the Quality Manual. The individual serving in this capacity, irrespective of other responsibilities, has responsibility and authority that includes:
• Ensure that processes needed for the Quality System are established, implemented and maintained,
• Report to top management on the performance of the Quality System and any need for improvement, and
• Ensure the promotion of awareness of customer requirements throughout the organization.
b. Control quality related documents and records as described in sections 4.2.3 and 4.2.4 of the Quality Manual and the quality procedures, (QP4.2.3 and QP4.2.4), referenced.
c. Schedule, conduct and maintain records of Management Review as described in section 5.6 of the Quality Manual and in the quality procedure (QP5.6) referenced.
d. Provide management with information regarding resources required to properly maintain the Quality System and meet MSA's and customer's quality requirements as described in sections 6.1 and 6.2 of the Quality Manual. These resources include the training of personnel performing activities that affect quality
e. Ensure that the accuracy of all devices used to monitor or measure product quality is maintained as described in section 7.5 of the Quality Manual.
f. Manage the Internal Audit system as described in sections 8.2.1 and 8.2.2 of the Quality Manual and the quality procedure (QP 8.2.2) referenced.
g. Maintain systems established to drive continuous improvement of the Quality System as described in section 8.5 of the Quality Manual and the quality procedure, (QP8.5.2) referenced.
• Production Support
a. Clarify quality requirements for production by providing photos, samples and instructions as needed.
b. At the request of the Shift Supervisors, assist in any training of Inspectors /Packers to help them to be able to identify quality products and to perform each job according to most recent CBAs.
• Monitoring and Measurement
a. Perform daily product verification and enter product measurement data into SPC program. This data is essential for product validation.
b. When nonconforming product is detected, implement procedures for identification, isolation, documentation and disposition (QP8.2.4 Monitoring and Measurement of Product and QP 7.5.3 Identification and Traceability.)
c. Control nonconforming product using the inventory program (Cyframe)
• Samples
a. Ensure the integrity of the entire Legacy and retain sample library.
b. Regularly monitoring and reviewing all samples to confirm all meet specifications.
c. Supervise the selection, maintenance, storage and disposition of product samples.
• Document Control
a. Ensure Job Books in the QA Lab are maintained according to established procedures.
b. Ensure current computerized records for each Job Book.
c. Ensure appropriate revision number of obsoleting of old materials is matained.
d. Regularly review documents revise to improve or optimize design and utilization.
Associates degree or 5+ years in a similar quality assurance program, department, or operation is preferred. Further education a plus.
Experience working in the quality area for an organization certified to SQF, ISO 9001 or similar standards.
Knowledge of Quality Assurance system development and implementation such as SQF, ANSI/ISO/ASQ 9001, ISO 14001, QS 9100, etc.
Experience with the proper use of measuring equipment including gram scale and hand-held micrometer