Maintenance Manager
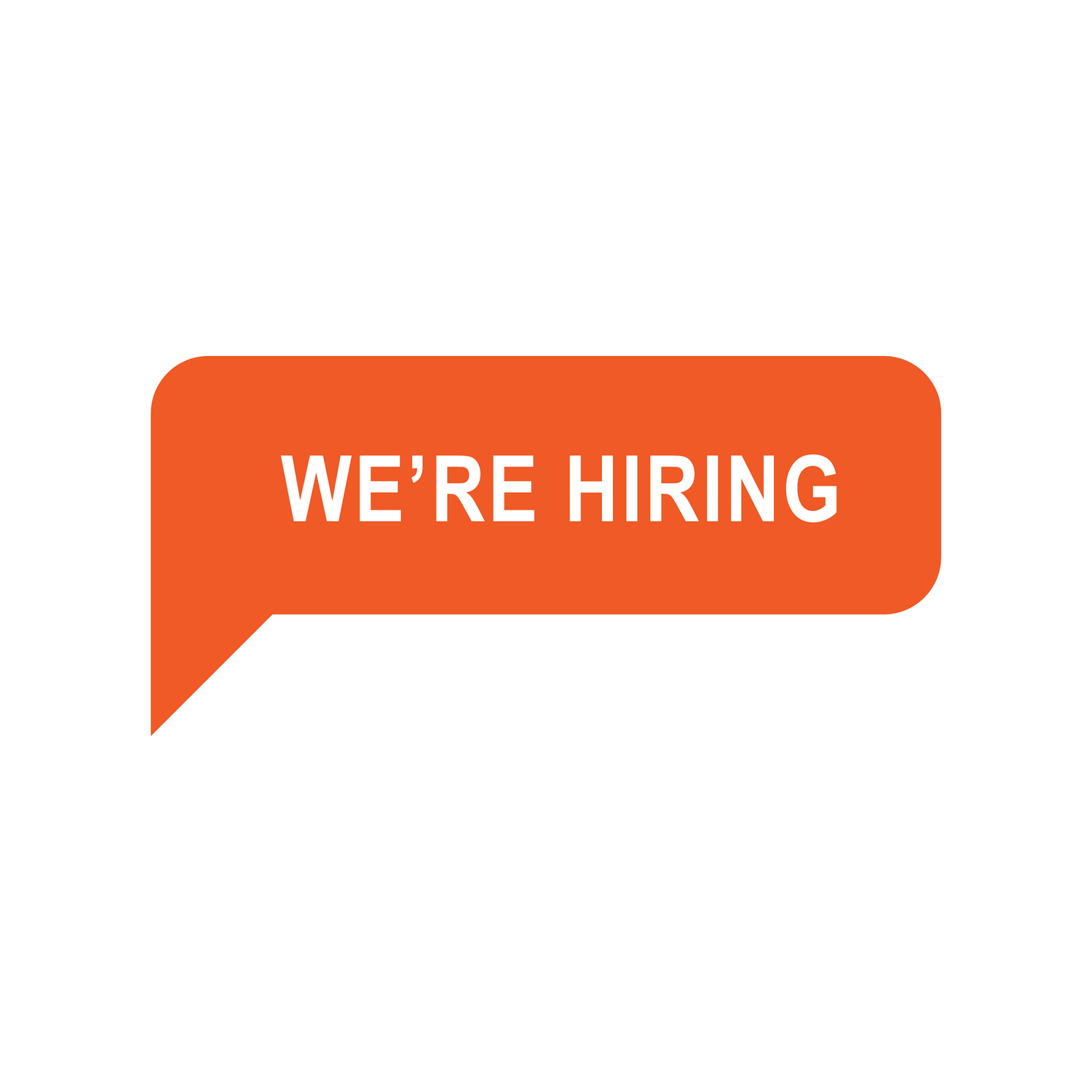
Red Collar Pet Foods, Inc.
2021-12-03 07:32:02
Joplin,
Missouri,
United States
Job type: fulltime
Job industry: Executive Positions
Job description
Job Location:: Joplin, MO - Joplin, MO
Red Collar Pet Foods is looking for a Maintenance Manager to join our exciting new pet food business at one of our manufacturing plants. Who is Red Collar? We are pet people, and to us pets are family. We believe that they deserve good food made with wholesome and balanced nutrition in every bag and bowl. It is our commitment to quality ingredients and manufacturing exclusively in the U.S. which makes us all proud of our company and the pets we ultimately feed.
As part of our overall total compensation package, Red Collar Pet Foods offers a competitive benefits package to all associates which includes: Medical, Dental, Vision & Life Insurance, Short- & Long-Term Disability, and 401k match. Associates are also immediately eligible (based on hire date) up to three weeks of vacation, Paid Holidays per year, Sick Pay, Maternity & Parental Leave, and annual/quarterly bonus earning potential, plus many other ancillary benefits not listed here.
Purpose of Role
The Maintenance Manager reports to the Plant Manager with a functional dotted line reporting relationship to the centrally located Senior Technical Manager. This position utilizes sound people management, technical problem solving and project management skills to preserve and maintain the factory's infrastructure, utilities and equipment. It requires adherence to global maintenance best practices, including continuous improvement and total productive maintenance (TPM). Must provide technical solutions for plant issues along with managing the storeroom to achieve department objectives. This position manages both internal and external resources to support activities on the site. This position also actively participates and contributes to the success of area continuous improvement teams, factory operating system and underpins the site security, safety, and environmental programs.
Principal Accountabilities
- Conversion. Actively participate and collaborate with all functional areas to properly maintain and improve the plant assets to deliver metrics (Quality, Safety, Plant Service Level (PSL), TRS, productivity, waste reduction, etc.) within the assigned area.
- Change Agent - Acting as the catalyst, identify opportunities for site technical or operations improvement, gain acceptance of the need for change and lead the implementation of the agreed upon changes.
- Associate Advocacy - Effectively manage direct reports to ensure global maintenance best practices are being implemented and adhered to. Ensure that each direct report has results-based objectives, timely performance reviews, and appropriate development plans.
- Ensure that each maintenance associate has the necessary skills and tools to meet their job expectations. Develop a robust plan for skills enhancement for all maintenance associates. Drive team engagement through conducting impact sessions/follow-ups, as well as ensuring all team members have robust development plans.
- Technology Advancement - Site technical champion for commissioning, validating and start-up (CVS) of all new capital projects. Ensure involvement of all maintenance associates in the CVS process. First point of contact for all engineering projects.
- Area Strategy - Manage Maintenance costs to ensure adherence to the existing budget. Provide timely and accurate maintenance cost analysis to ensure the budgeting process is accurate and meets the business requirements. Participate in all site projects to ensure that safety, reliability, maintainability, and cost effectiveness requirements are delivered. Key stakeholder in identifying and prioritizing site capital needs. Write, justify, submit and execute site capital projects as approved. Provide Safety, Security, and Environmental advice/counsel to site staff regarding issues which may have an impact on the site. Operations Strategy - Align with operations partner(s), providing key maintenance requirements including shutdowns and mandatory down-time requirements, to ensure overall equipment effectiveness and support of site operations objectives (ATS, TRS, RFT, etc.)
- Personal Development - Actively participate in the associate development process to remain current in managerial and technical competencies. Clearly de?ne and develop career goals and objectives.
- Other duties and responsibilities as assigned.
Key Functional Skills/Knowledge
- Working knowledge of Programmable Logic Control
- Working knowledge of Electrical Systems
- Working knowledge of Mechanical Systems
- Working knowledge of compressed air system and components
- Working knowledge of boilers
- Working knowledge of Preventative Maintenance Programs and Systems
- Ability to convey communications clearly and concisely
- Must be capable of working at elevated heights and or con?ned space
- Wearing proper personal protective equipment (hair net, bump cap, ear plugs, safety shoes, and uniform) Bending, stooping, twist, turn, standing for extended time periods, reaching, climbing stairs, and lifting up to 55 lbs.
- Must be able to adapt to temperature and environmental extremes such as hot to cold, dust dirt and chemicals
Qualifications
- An undergraduate degree or equivalent, preferably in one of the Engineering, basic sciences or business related disciplines
- 7+ years' experience in a Manufacturing Environment in a Maintenance capacity
- 2+ years' experience in a supervisory or managerial role
Preferred Quali?cations:
- In-depth knowledge of critical utility systems (steam, air, water, electricity)
- Experience with Reading Electrical Blue Prints (?ow diagrams, P&ID's, schematics)
- Highly developed understanding and proven experience in all aspects of safety in the work-place Minimum 1 year experience in a food production environment
- Minimum 7 years in a Production Environment
- Minimum 5 years in a supervisory or managerial role
- Cross-Functional Managerial experience (operations, HR, Engineering, etc.)
- Proven Project Management experience
- Experience with planning and managing a site's maintenance budget
- Pro?ciency in word processing, spreadsheets, internet software, e-mail
- Ability to work any shift as needed
- Ability to tolerate an ambiguous environment
- Working knowledge of OSHA/EPA requirements and related guidelines
- Working knowledge of Lock Out Tag Out Procedures
- Working knowledge of property protection insurance requirements
- Advanced degree preferred, but not required
Red Collar Pet Foods is an equal opportunity employer and all qualified applicants will receive consideration for employment without regard to race, color, religion, sex, sexual orientation, gender identity, national origin, disability status, protected veteran status, or any other characteristic protected by law. If you need assistance or an accommodation during the application process because of a disability, it is available upon request. The company is pleased to provide such assistance, and no applicant will be penalized as a result of such a request.
PI