PRODUCTION SUPERVISOR
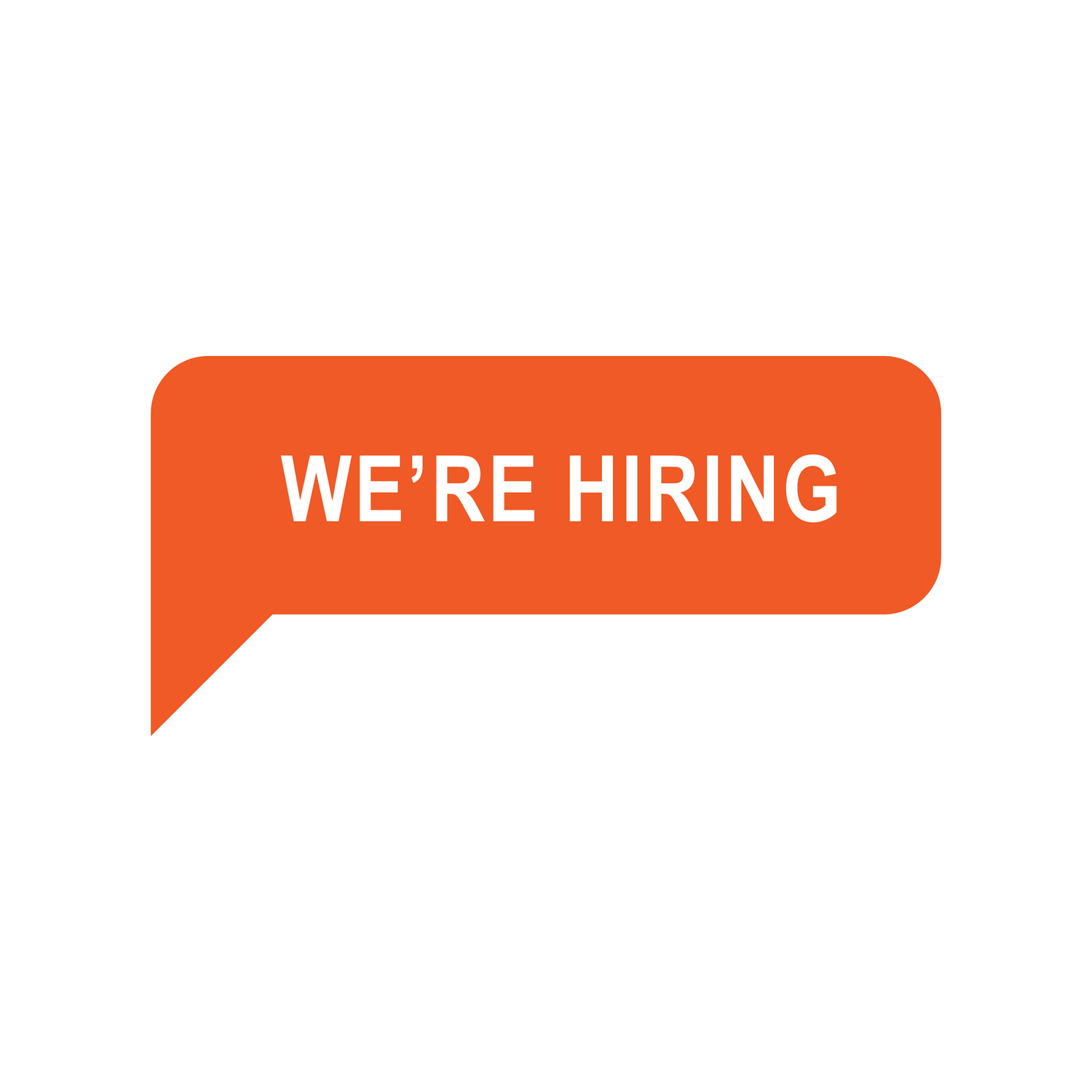
Berry Global, inc
2021-12-04 01:00:03
Pryor,
Oklahoma,
United States
Job type: fulltime
Job industry: Manufacturing Operations
Job description
Overview:
Berry Global Berry Global, headquartered in Evansville, Indiana, is committed to its mission of 'Always Advancing to Protect What's Important.' With $13 billion in revenue for fiscal year 2019 on a combined pro forma basis from operations, Berry is a leading global supplier of a broad range of innovative nonwoven, flexible, and rigid products used every day within consumer and industrial end markets. Berry operates over 290 manufacturing facilities worldwide, on six continents, and employs over 48,000 individuals.
At Berry, we pursue excellence in all that we do and are always advancing to improve the way we work along with the products and services we provide. Our culture fosters trust and partnerships through appreciation, acknowledgement, and inclusion. At Berry, we are continuously improving to support our mission and exemplify our values of partnerships, excellence, growth, and safety. To learn more about Berry, visit (url removed)
Qualifications:
Special Skills:
Ability to read and interpret documents such as safety rules, operating and maintenance instructions, procedure manuals , order forms and checklists
Ability to complete routine reports and correspondence
Ability to speak effectively with co-workers or groups of co-workers, supervisors or others within the company
Ability to add, subtract, multiply, and divide in all units of measure, using whole numbers, common fractions and decimals
Ability to compute rate, ratio and percent and to draw and interpret bar graphs
Ability to apply common sense understanding to carry out detailed, but uninvolved written or oral instructions
Ability to deal with problems involving a few concrete variables in or from standardized situations
Work Environment:
This position requires that the employee be able to work
Outdoors 1/3 of the time or less
Near moving mechanical parts over 2/3 of the time
High or precarious places 1/3 of the time or less
Near electrical components 1/3 of the time or less
Near vibrating equipment and tools 1/3 of the time or less
Fumes from equipment or airborne 1/3 of the time or less
particles
Toxic or caustic chemicals 1/3 of the time or less
Extreme heat (non-weather) 1/3 of the time or less
Extreme cold (non-weather) None
Wet or humid conditions (non-weather) 1/3 of the time or less
Loud environments (equipment operation) 1/3 of the time or less
Essential Physical Requirements:
Walking to inspect facility including raw materials, work-in-process and finished goods, building and equipment, and overall manufacturing and warehouse operations for as much as 100% of workday
Sitting to prepare reports and use computer equipment for approximately 10% of workday
Must be able to assist with set-ups and mechanical repairs which can require
Standing for as much as 100% of workday
Reaching with hands and arms for as much as 75% of workday
Climbing or balancing for as much as 25% of workday
Kneeling, stooping, crouching or crawling for as much as 10% of workday
Bending, twisting, reaching and leaning for as much as 75% of workday
Talking to communicate with direct reports for as much as 100% of workday
Hearing to communicate with direct reports for as much as 100% of workday
Using arms to grasp, handle and type for as much as 75% of workday
The employee in this job is required to exert 60 pounds of force occasionally (less than 1/3 of time); and/or up to 40 pounds of force frequently (1/3 to 2/3 of time); and/or up to 30 pounds of force regularly (more than 2/3 of the total time)
Education:
High school diploma or equivalent (GED) preferred.
Experience:
Minimum of 5 years manufacturing experience in required
Minimum 2 years leadership experience required
Experience with Cast and/or Blown film extrusion preferred
Special Skills:
Ability to use good judgment and motivate others
Ability to adapt to changes in the work environment
Computer literate
Ability to define problems and seek out appropriate help for resolution
Must be able to coordinate multiple tasks
Note: This job description in no way states or implies that these are the only duties to be performed by the Assistant Production Manager.
Responsibilities:
Primary Function:
Responsible for the supervision and direction of hourly production employees. Operate the department within all safety regulations, quality standards and maintain production standards as efficiently as possible. Will assume responsibility for the department in the absence of the Production Manager. Will maintain the highest standard of professionalism and maintain a positive attitude while handling multiple tasks and priorities.
Essential Functions:
Staff planning to ensure adequate coverage on all machines for scheduled production
Maintain good employee relations by stimulating maximum efficiency and productivity of all production employees through good communication and regular performance reviews
Provide training as appropriate (i.e. tool box meetings, safety, etc.)
Recommend the hiring and releasing of production personnel as required to maintain production schedules
Responsible for all processes, equipment, employee's safety and housekeeping of the areas and meeting production quality and quantity standards of their shift
Ensure the machines run according to the instructions/specifications on the Traveler (i.e. correct resin, additives and packaging)
Provide detailed reports to Production Manager and/or Plant Manger
Correctly record daily production to Web EFF
Communicate with other supervisors to anticipate issues and ensure smooth a transition from shift to shift
Assure efficient and economical utilization of materials, improvement of methods and elimination of wasteful practices within the departments
Keep accurate records of departmental activities
Collect and summarize raw material usage and inventory, monitoring usage for maximum efficiency
Perform duties in a safe manner and address all observed safety hazards and unresolved safety issues with the appropriate personnel
Coordinate with the Plant and/or Production Manager, EHS Representative and Maintenance Manager on maintenance priorities
Safety Commitment:
Takes reasonable care for their own health and safety.
Takes reasonable care for the health and safety of others.
Authorized to stop work when a perceived unsafe condition or behavior may result in an unwanted event
Understands and actively participates in the company's EHS policy, goals, and objectives
Additional Front Line Leader Responsibilities:
Accountable for the safety of all employees for whom they are responsible through active engagement in safety activities and provides clear, consistent communication of safe work expectations
Supports and investigates situations in which line/equipment stoppage occurs due to perceived, imminent safety risk
Completes responsibilities in accordance with the organization's policies and procedures, and applicable laws
Actively leads risk assessment activities for their area of responsibility by driving prioritized corrective and preventive actions to eliminate/reduce environmental health or safety risks
Lead all required meetings with safety (i.e. Pre-shift, Department, Change Management, General communication, Town Hall, etc.)
Completes incident investigations, root cause analysis and implements corrective actions accordingly in a timely and thorough manner.
Ensures the proper training and development of all assigned employees for whom they are responsible
Sets goals for their organizational unit; achieves goals and ensures that all employees understand and work toward achieving goals.
Motivates and coaches employees through good communication and frequent performance feedback. Identifies and coordinates additional training as needed.