Developmental Operations Manager
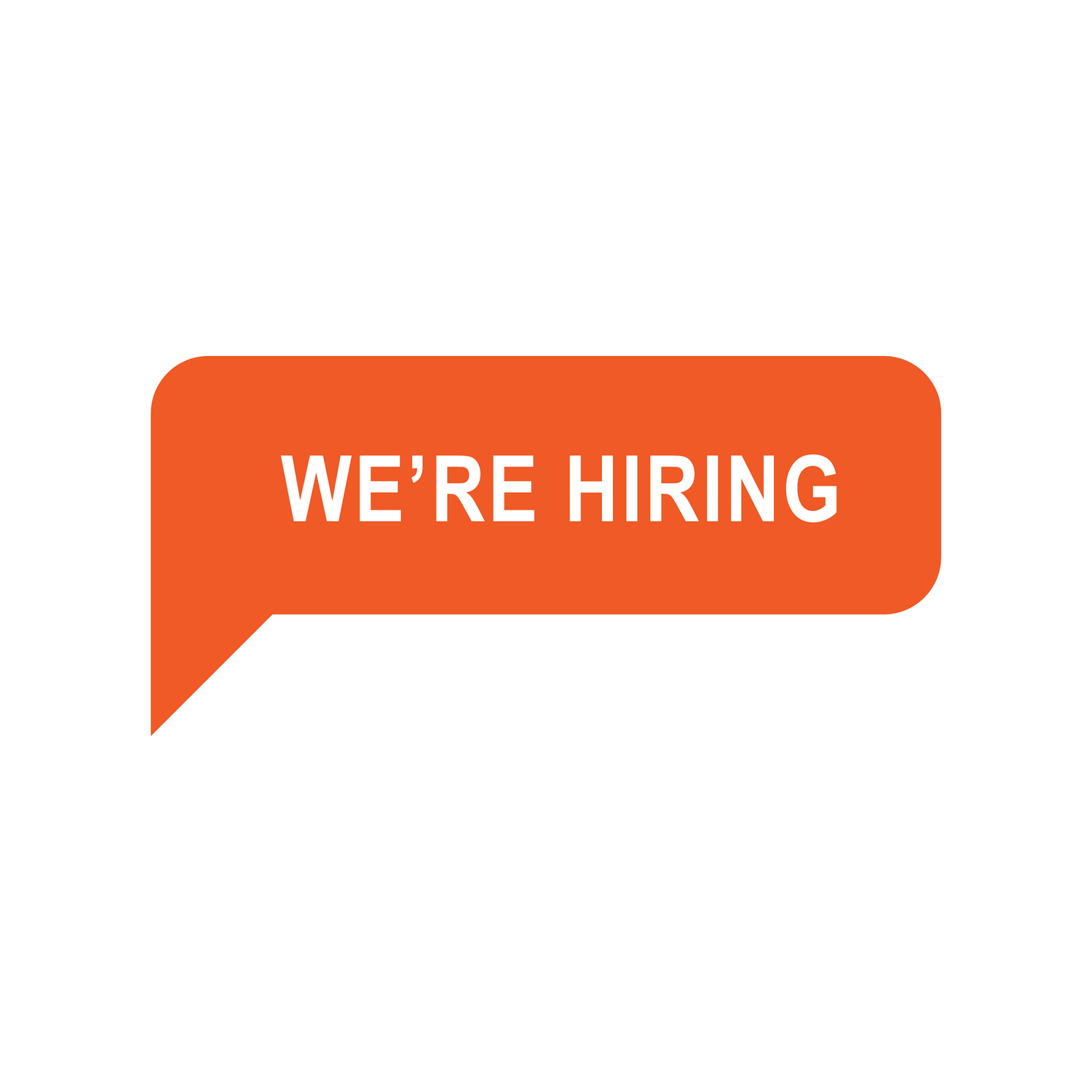
Valmont Industries, Inc.
2021-12-03 07:45:11
Houston,
Texas,
United States
Job type: fulltime
Job industry: Manufacturing Operations
Job description
6123 Cunningham Rd Houston Texas 77041
Why Valmont
Welcome to Valmont, where a world of opportunity awaits. When you join our team, you become part of a passionate group dedicated to changing lives and conserving resources around the globe. We want problem solvers who roll up their sleeves to foster progress and innovation for all people. At Valmont, we provide infrastructure, irrigation, tubing and coatings to the world. We strengthen cities. We nourish croplands. We design, manufacture and coat. Our products and services make a difference. Join us, and BUILD YOUR WORLD.
A Brief Summary of This Position:
The Developmental Operations Manager is a Manager level role within Valmont's Coatings Division. The incumbent must be a highly driven individual who is a confident, hands-on, and independent self-starter with a strong OEM (Original Equipment Manufacturer) manufacturing or industrial coatings background to join the organization and acquire the skills and experience necessary to lead a galvanizing company. This position manages a two or three shift operation including oversight of safety, production, quality, shipping and receiving, scheduling, maintenance, chemical reclamation, lean implementation and initiatives, and compliance reporting. This high potential position demonstrates the ability and self-discipline to carefully and accurately run multiple departments, as well as has a desire to advance quickly in an organization. This developmental position is designed to support the growth and expansion of our business and organization.
Essential Functions:
Manage the use of plant resources to ensure that all plant operations are meeting or exceeding safety, quality, and production goals set by the General Manager
Oversee the production operations of a galvanizing facility
Receive intense training in industrial troubleshooting, accounting, financial forecasting, human resources, and galvanizing sales and services
Assist in identifying operations' best practices, performing lean audits and kaizen events, and travel occasionally to assist/learn from high level project management experiences
Within two to four years, the successful Operations Manager will be expected to transition into a higher level position running his/her own site somewhere in the US with full Profit & Loss (P&L) responsibility - including oversight of operations, sales, accounting, lean implementation, HR and engineering
Facilitate positive customer relations through the services of quality coated product and on-time delivery
Utilize production and other analytical reports to better gauge plant performance and to make better decisions
Review and control operation expenses for raw materials, operating supplies, and equipment
Maintain manpower requirements through proper staffing, training, and development of production employees, supervisors, and other technical personnel
Ensure compliance with environmental and safety requirements as specified by corporate policy and government regulation
Other Important Details about the Role:
Plan and develop plant personnel to produce maximum efficiency and utilization of available resources
Select, train, develop and motivate an effective staff to assure the profitable attainment of present and future safety, production, quality and service objectives
Travel to other Coatings sites and assist in identifying operations' best practices, perform lean audits, and assist with the setup and operation of Greenfield (startup) or satellite operations
Required Qualifications of Every Candidate (Education, Experience, Knowledge, Skills and Abilities):
Bachelor's degree with 6+ years of relevant experience, Associates degree with 8+ years of relevant experience or 10+ years of relevant experience
The ability to recognize and solve practical problems or issues
Prior supervisory experience
Proven track record in lean manufacturing principles including standard work, continuous improvement, problem resolution and delivery of results positively affecting the bottom line of the organization
Ability to travel approximately 10-15%
Ability and willingness to relocate as required
Ability to occasionally lift up to 15 pounds, although most frequent lift is up to 10 pounds
Ability to wear all required PPE for the production facility, as well as be exposed to outdoor weather and indoor facility conditions including cold, heat, dirt, noise and fumes
Must be a person of passion and integrity who has the drive to excel and deliver exceptional results
Highly Qualified Candidates Will Also Possess These Qualifications:
Master's in Business Administration Industrial Management, Manufacturing, Operations, Engineering or Chemistry
Minimum 5-7 years of supervisory or management experience overseeing employees in a number of functional areas in an industrial environment
Previous experience in galvanizing or a coatings company would be ideal, but is not necessary
Working knowledge of OSHA and environmental regulations as well as state and federal labor standards
The ability to read and interpret documents such as safety rules, operating and maintenance instructions, and procedural manuals
Strong leadership skills and the ability to support divisional business objectives
The ability to communicate and interact with coworkers in a professional manner
Six Sigma Green or Black Belt Certification
Working Environment and Physical Efforts:
Some of the working conditions for this position is in a manufacturing shop environment with exposure to dirt, grease, fumes, cold, heat, noise, dust. The Operations Manager will work in both the office and shop environment. Environment is fast paced and demanding most of the time. 10-15% travel is required for this position. Incumbent must utilize proper ergonomic safeguards such as monitor height and positions, keyboard location and height and proper wrists rests. The employee must occasionally lift and/or move up to 15 pounds in working with large files, binders, and computer equipment. Specific vision abilities required by this job include close vision, distance vision, peripheral vision, and depth perception.
Valmont does not discriminate against any employee or applicant in employment opportunities or practices on the basis of race, color, religion, sex, sexual orientation, gender identity, national origin, age, genetic information, veteran status, disability or any other characteristic protected by law. Reasonable accommodation may be made to enable individuals with disabilities to perform the essential functions.
If you have a disability and require any assistance in filling out the application for employment email .