Maintenance & Reliability Manager
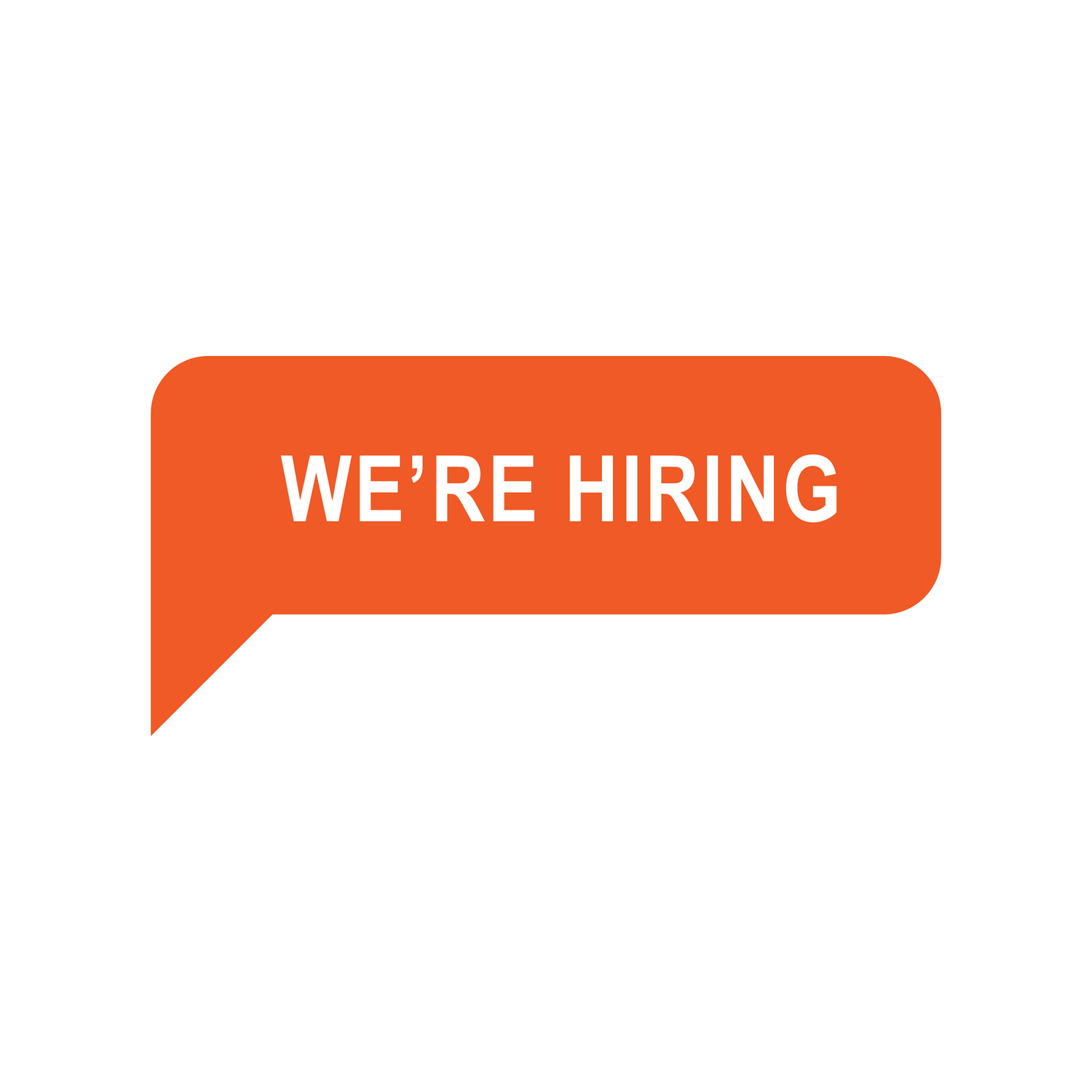
Hargrove Engineers + Constructors
2021-12-04 01:00:03
Port Neches,
Texas,
United States
Job type: fulltime
Job industry: Construction
Job description
Overview:
This role will drive vision, provide direction, set priority and lead the Mechanical Maintenance Team site wide across multiple PSM manufacturing units on its journey to achieve World Class Maintenance and Reliability Performance based on benchmarked industry standards at Client's Port Neches Site. Manages asset reliability risks, contributes technical equipment assistance, supports improvement programs and provides Mechanical Maintenance for all assets. Ensures production equipment reliability to enable manufacturing processes to meet requirements with regards to Safety, production volume, cost, and quality. Supports production OEE expectations by completing PM schedules and maintaining key spare parts on site to avoid excessive downtime due to unexpected equipment failures. Direct reports include a Maintenance Mechanical Engineering Team Lead, Mechanical Maintenance Team Leads, Central Shops and a Pipe/Weld Fabrication Shop. Indirect reports include Machinists, Pipe Fitter/Welders, Rotating Equipment Specialists, Mechanical Engineers and a Central Shop's Planner. This position reports to the Site Maintenance Sr. Manager.
Responsibilities:
The individual must be a proven leader who can provide vision, lead and achieve daily, yearly and long term asset reliability, safety and cost goals through application of Maintenance best practices site wide. The individual must have a good working knowledge of maintenance, reliability, PSM and MIQA best practices. This person must have the organizational capability to work across multiple businesses, supply chains and systems and be able to communicate well with operators, mechanics, peers and leadership. They must be able to lead multiple improvement teams and network with appropriate professional organizations and technical organizations such as the Rotating Machinery, Process Equipment and M&RS.
Requires presence in the workplace on a regular basis and an ability to work extra hours if needed. Must be available by phone 24/7.
Leadership
Lead efforts to ensure reliability and maintainability of safety systems, environmental control systems, equipment, processes, utilities, facilities, infrastructure and controls.
During unscheduled events and planned maintenance outages, acquire appropriate resources, and help coordinate and direct all aspects of maintenance workflow.
Maintain a metric dashboard for maintenance that drives improvement and helps prioritize actions.
Provide leadership to achieve cost competitive World Class Maintenance and Reliability Performance and Efficiency based on benchmarked industry standards.
Develop and maintain a 3 year improvement plan for the maintenance team with milestones and programs.
Manage site maintenance attrition forecasting and plan for hiring. Lead the selection, assignment, development, coaching and performance evaluation of the Mechanical Engineers, Maintenance Team Leads, Rotating Equipment Specialists and Craftsmen.
Participate in the Site Maintenance Leadership Team (SMLT) responsible for setting site policies related to Maintenance personnel and processes. This Team also establishes and drives overall vision and direction for site wide maintenance improvement programs that reduce cost and improve asset reliability.
Partner with human resources department to manage maintenance craft unions labor relations, including participation in collective bargaining process. Serve as a 2nd chair bargaining representative for site maintenance in the PF/Welder and Machinist Unions.
Develop self, direct reports, and other leaders and subordinates. Keep current with technical developments in Asset Management through study, trade journals, technical societies, and seminars.
Assist other employees in accomplishments of company goals.
Follow instructions and perform other duties assigned by supervisor.
Work Management Process
Institutionalize best practices in the Work Management Processes (WMP) supported by a Computer Maintenance Management System (CMMS) and other associated tools.
Drive improvement programs that achieve a more proactive work management process and a stronger relationship between maintenance activities and business cost performance.
Safety Health & Environment / Process Safety Management (PSM) / Mechanical Integrity Quality Assurance (MIQA)
Participate in Environmental, Health, & Safety initiatives as set forth by the company.
Contribute with managerial and leadership expertise to events that impact the safety, health and environmental performance of the site. Lead in the promotion of a strong safety and environmental stewardship culture.
Participate in and complete company-required training programs.
Ensure good engineering practices including RAGAGEP and API standards are followed.
Provide support for PSM, MIQA and SIS initiatives.
Ensure area MIQA systems meet the requirements of OSHA Process Safety.
Reliability
Oversee and participate in the development of engineering solutions to repetitive failures and other problems that adversely affect plant manufacturing operations. These problems include capacity, quality, cost or regulatory compliance issues.
Support PNO Reliability efforts in root cause analysis, recording equipment history, loss elimination, risk management, life cycle asset management, and Preventive and Predictive Maintenance programs.
Provide support for the PNO Reliability Team and CAPEX initiatives.
Work with project engineering and technical management to ensure the reliability and maintainability of new and modified installations. Participate by providing resources, criteria for the evaluation of equipment, information on technical MRO suppliers and information on technical maintenance service providers.
Budgeting and Cost Management
Develop yearly and monthly maintenance budgets and the activities to ensure alignment and achievement of these budgets.
Develop a strong cost management structure for Maintenance that identifies improvement opportunities including both short and long term actions to reduce/optimize cost.
Participate in budgeting activities, review costs and expenses and strive for continuous improvement maintenance costs. Apply value analysis to repair/replace, repair/re-design, and make/buy decisions.
Turnaround Planning and Execution
Provide support as needed for Turnaround (TAR) planning and execution.
Qualifications:
Education: Bachelor's in Mechanical, Chemical, or Electrical Engineer
Specific education or experience:
10+ years reliability/maintenance experience in a petrochemical or refining facility
5+ years of reliability, maintenance and/or supervisory experience in a petrochemical or refining facility
Six Sigma certified as Black Belt preferred
Specific certifications, licenses, or registrations:
Must be able to obtain and maintain current TWIC certification
Must have a level of proficiency with Internet, Email, and Microsoft programs
Support the manufacturing areas 24/7
Requires climbing ladders and accessing scaffolding.
Requires a broad knowledge of engineering principles governing petrochemical operations. Must have experience (10+years) in the chemical industry with extensive background in plant operations and equipment. Possess the ability to coordinate the activities of personnel in all matters necessary to run in a safe environmentally compliant reliable and efficient manner.
Must have high technical and analytical abilities to handle operational problems and plant compliance concerns with quick diagnosis and prompt decisions. Must have the ability to motivate and influence people. Good communication and diplomacy skills as this position will work with employees at all levels of the organization.