Quality Supervisor
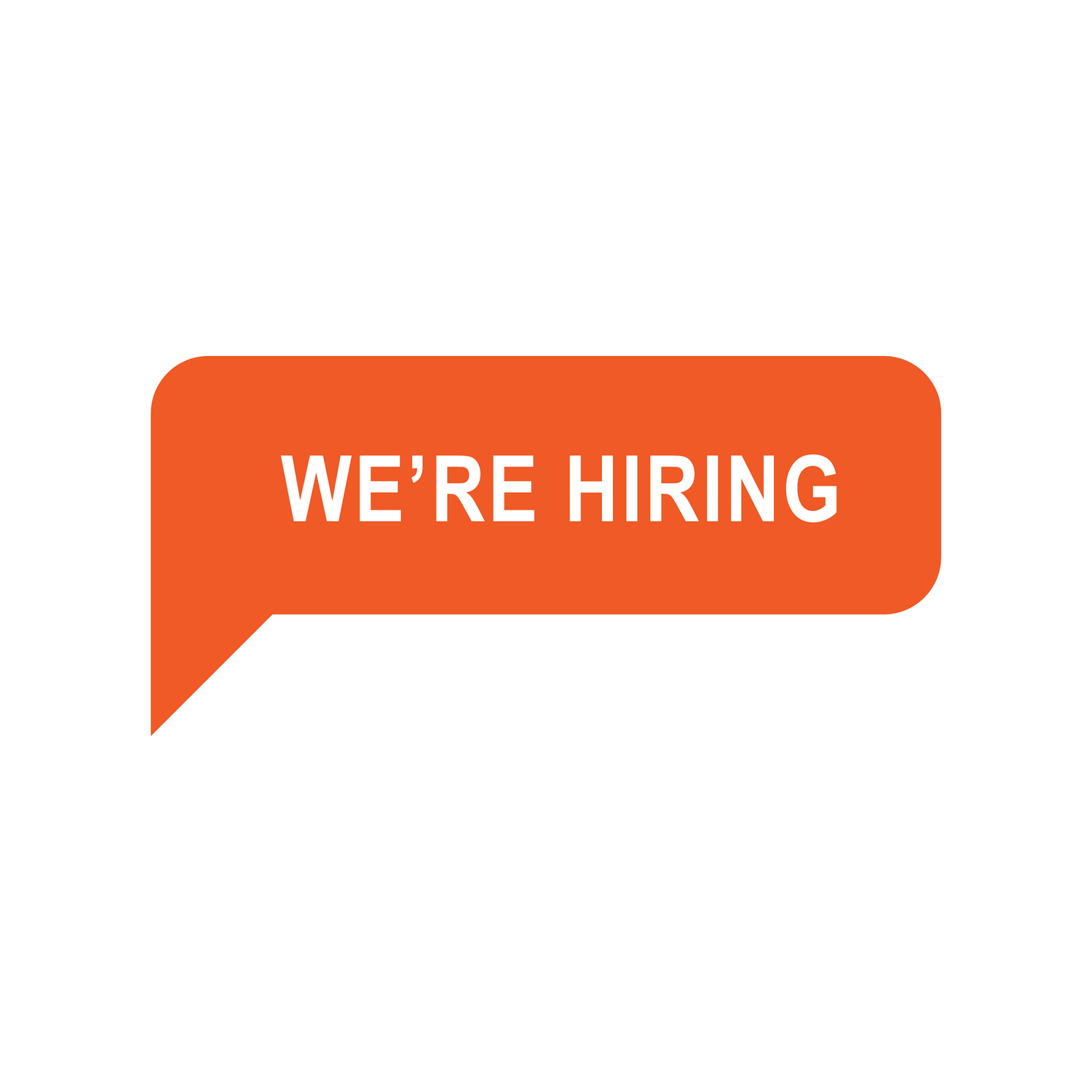
Silver Spring Foods, Inc.
2021-12-03 07:32:03
Eau Claire,
Wisconsin,
United States
Job type: fulltime
Job industry: Science & Technology
Job description
Silver Spring Foods, Inc., located in Eau Claire, WI, provides premium specialty products for food enthusiasts to embolden cuisine and make food more flavorful.
Silver Spring Foods is the world's largest grower and processor of horseradish. We've been adding "zing" to food for over 90 years. We take pride in the products we make and believe in the enrichment of people's lives. We provide farm-to-table mustards, sauces, and horseradish products. Our state of the art manufacturing facility, private label experience, and production versatility position Silver Spring as a premier co-packer.
Job Description Summary
The basic function of the Quality Supervisor is to supervise and support the maintenance of strict quality control standard for the Operations Department, ensuring that food safety practices are followed throughout the production process. Responsible for supporting activities to ensure food safety, integrity, legality and quality by serving as a member of the following internal groups:
- Food Safety Team
- Corrective Actions Team
- Production Management
- Quality Task Force
- Food Security/Defense
- BRC Team
Duties and Responsibilities
The duties and responsibilities of a Quality Supervisor shall consist of, but not be limited to the following:
- Ensures that all formulas and finished product are monitored on a scheduled basis to maintain set quality control standards.
- Ensures that product is sampled for microbiological testing as required and microbiological results are within specifications.
- Works in cooperation with Research & Development in determining efficient testing and/or inspection points, timetables, and frequencies.
- Reviews reports for out of spec results and works with other departments to address as necessary
- Ensures that the Quality Manager is kept informed of daily results or any lapse or potential lapse in quality standards.
- Directly supervises the activities & actions of the Quality Control Technicians, Quality Auditors, QA Inspectors and QA Specialists.
- Responsible for training, scheduling, coaching and handling corrective actions for Quality Control Technicians, Quality Auditors, QA Inspectors and QA Specialists.
- Completes performance evaluations on direct reports as specified by the company policy.
- Responsible for conducting quality audits of the facility to ensure compliance with the locations policies and procedures.
- Ensures completion of CCP documentation and any CCP related corrective actions.
- Maintains the calibration program for all lab equipment.
- Assists Quality Manager with the development and implementation of quality policies and procedures necessary to ensures compliance with intent of the BRC standard
- Assists Quality Manager with plant wide quality and food safety training.
- Assists Quality Manger in the investigation of consumer complaints, product non-conformance and internal non-conformance.
- Periodically evaluates all equipment for defect that could lead to quality control problems. Makes recommendations for repair or replacement to the Quality Manager.
- Actively participates in all inspections including customer, third party, state, and federal.
- Ensures that any pests or pest control issues are quickly handled routinely and monitored for effectiveness.
- Respects the confidentiality of customer and employee information.
- Stresses the importance of safety on the job to all employees.
- Conducts DuPont STOP Safety Audits.
- Establishes and maintains a cooperative, professional, and positive working relationship with all personnel and management levels. Ensures that effective working relationships are established among the Quality staff and other departments for clear open lines of communication
- Supports and enforces company guidelines, policies, procedures, and work rules in a consistent, professional manner. Demonstrates good judgment and reasoning when investigating and solving problems; shows ability to tactfully handle difficult situations.
- Meets regularly with all assigned personnel in an effort to keep them informed of general activities and any pertinent information required for efficient operation on a daily basis.
- Recommends training programs to ensure Quality personnel are well aware of their duties, authority and responsibility.
- Performs all duties in an independent manner with minimal direction and supervision.
- Recognizes and performs duties which need to be performed although not directly assigned.
- Performs work duties and responsibilities in accordance with Good Manufacturing Practices.
- Is flexible to work hours beyond and/or outside regular schedule to ensure proper coverage for the position when needed.
- Demonstrates behaviors in accordance with the 30 Fundamentals of the Huntsinger Way.
- Performs additional duties & responsibilities as necessary.
Requirements
Education & Work Experience
Required: High school diploma and three to five years' experience in quality or laboratory for a food processing company, or related work experience, along with supervisory experience.
Preferred: Associate or Bachelor of Science degree in microbiology, food science, biology or other related science field. Five to seven years' experience in quality or laboratory for a food processing company or related work experience, along with supervisory experience.
Licensing, Registration, Certification
Required: Drivers license
Preferred: HACCP Training Certification, GFSI Certification (BRC Preferred), PCQI Certification
Skills, Knowledge and Abilities
- Familiar with all basic aspects of quality control.
- Needs to understand basic microbiology, equipment hygiene practices, & product shelf life.
- Must have ability to understand and interface with production operations.
- Strong computer skills
- Supervisory skills
- Understands how to deal effectively with people at all levels
- Demonstrates effective problem solving, root-cause analytical skills
- Strong organizational skills
Physical, Mental and Visual Skills
- Sitting, standing, walking, bending, stooping, climbing over obstacles.
- Ability to lift up to 50 lbs.
- Must hear well enough to converse on telephone, must see well enough to read reports.
- Must comprehend technical, microbiological reports, such as standard plate count, bacterial identification, and shelf life parameters.
- Must read and write English at High School level.
- Must be able to communicate ideas and instructions effectively both orally and in writing.
Working Conditions
Normal manufacturing environment with wet floors at times, and laboratory setting, both in and out of doors, noisy.
Annual Review
Job descriptions will be reviewed by the senior manager in the department to which the position belongs on an annual basis. Employees will be required to acknowledge/sign their job description on an annual basis.
We offer a competitive wage, along with a full benefits package, including medical, dental, 401(k) with company match, paid holidays, generous paid time off and a tuition reimbursement program.