Utility Plant Operator I
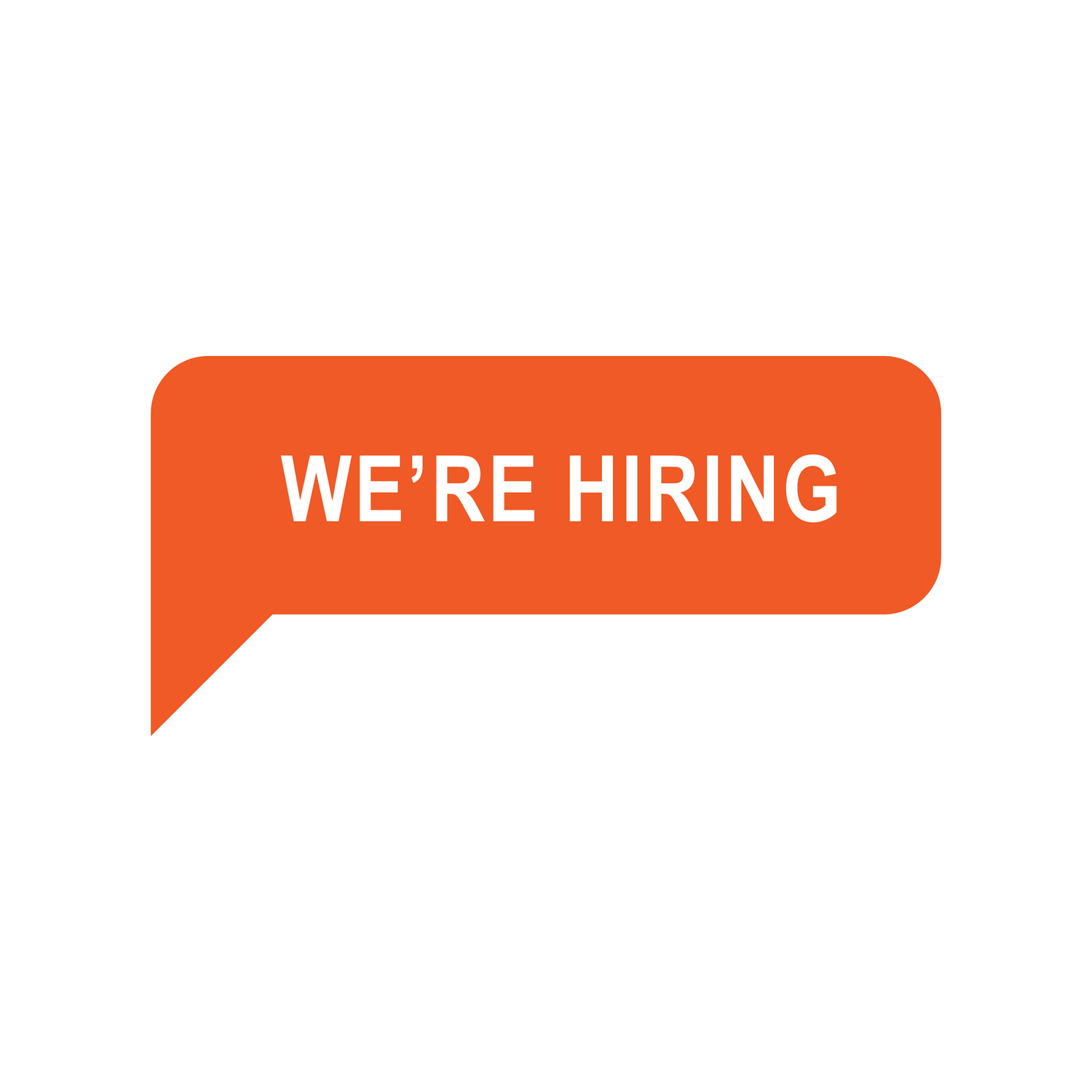
TalentBurst, Inc. 79949.00 US Dollar . USD Per annum
2021-12-03 08:58:50
South San Francisco,
California,
United States
Job type: fulltime
Job industry: Construction
Job description
Summary:
Utility Plant Operator I
06+ Months
South San Francisco, CA
The utility plant operator reports to the Facilities Supervisor and is responsible for the operation and maintenance of utility equipment supporting South San Francisco Production (SSFP) manufacturing.
Details:
Operate all utility systems and utility subsystems at Client, SSF. Performs installation, maintenance, repair, operation, and optimization of mechanical, plumbing, electrical equipment and systems supporting the Facility. Systems include: process equipment; HVAC/R; HEPA; clean utility system generation and distribution (RO/DI/PW/WFI and steam); process air systems; waste neutralization systems (process and biowaste); bulk chemical and gas systems; RW/Glycol Systems; Heating Hot Water.
Ensure all utility systems and utility subsystems at Client, SSF are operated and maintained in the following manner:
All preventative maintenance is performed at the appropriate interval and is completed by the assigned due date (adhere to all applicable SOP's).
All equipment remains in its designed cGMP and/or validated state at all times
All equipment operation is in accordance with Federal, State, local, and client regulations, procedures, and policies
Ensure/maintain all utility equipment areas in a constant state of inspection readiness; specifically but not limited to the following:
Cleanliness
Personnel and Equipment Safety
Compliance to cGMP requirements
Continuously evaluate the operation of all utility systems and utility subsystems at client SSF. Identify specific process improvement needs and provide recommendations for system upgrades.
Identify training deficiencies, provide recommendations for training and where applicable provide training.
Continuously evaluate all operational Standard Operating Procedures and Preventive Maintenance procedures for accuracy and applicability. Submit appropriate change requests through the Facility Services Document Tracking Data Base to correct any deficiencies discovered.
Provide operational support to Facility Services, Engineering, Manufacturing, and Research and Development. This support must not interfere with the normal day to day operation of any utility systems and utility subsystems at client SSF.
Perform Confined Space Entry on an as needed basis.
Complete preventive maintenance and assigned paperwork in a timely manner following all cGMP documentation guidelines.
Responsible for gathering and documenting the appropriate information associated with a System Discrepancy, (An event in manufacturing process and/or support system that is outside approved operating parameters or approved procedures).
Work with various chemicals, steam, pressurized gases/liquids of various temperatures.
Work in close proximity to moving equipment.
Conduct work in an FDA regulated environment.
Manage the day to day operation of the Utility systems including:
Point of contact for customer guidance and support.
Monitor the overall operation and status of the Utility Systems and submit work notifications for System repairs as needed.
Ensure all Utility rounds are completed and missed rounds are documented in the Utilities eLog
Responsible for ensuring rounds are completed at a minimum of once every twenty-four hours for GMP/Validated Critical Equipment.
Read the Utility eLog daily and ensure all relevant information is being documented.
Responsible for monitoring Utility work request queue and advancing notifications into work orders and completing all necessary TECOs. Managing work order queues from SAP as required.
Assist in troubleshooting efforts for all Utility Equipment that is directly impacting Manufacturing processes.
Must have the ability to work safely in an environment containing hazardous chemicals, high and low temperature liquids, high pressure liquids and gasses, steam, and moving machinery.
Ability to respond to and evaluate a variety of situations involving mechanical, electrical and systems controls
Ability to perform preventive maintenance and equipment servicing according to Standard Operating Procedures
Must have general knowledge of shop tool operation and safety.
Ability to read and Understand P&lDs, work from Standard Operating Procedures (SOPs) and have basic
computer skills using word processors, spreadsheets, databases, and email.
Must be detail oriented and demonstrate good record keeping practices.
Ability to work overtime or temporarily modify shift schedule to support manufacturing operations as needed.
Proficiency in understanding of Federal, State, Local and client regulations, procedures, and policies.
Working knowledge of electrical switchgear and distribution systems in the medium to low voltage range.
Demonstrate effective communication skills including preparing technical reports, the revision of various
procedures (SOPs, IPs, etc..) and the Utilization of the SAP work order system.
Ability to work with minimum or no supervision.
Education and Experience
High School diploma or equivalent. Technical degree, certificate, or coursework a plus.
2+ years of experience in an industrial / manufacturing maintenance role with demonstrated strong mechanical aptitude
Completion of relevant technical school, or accredited 2 year program may be considered in lieu of work experience.
Strong interpersonal skills are a must.
Proficiency in both oral and written communications is essential.
Work Environment/Physical Demands/Safety Considerations:
Attend all required cGMP training as required by Department Policy
Attend all required Safety training as required by Department Policy
Complete on the job training Using established training procedures
Work in standard office environment, GMP controlled environment, and utility maintenance areas.
Schedule could include a non-rotating 3/4-day (12 hour shift), one weekend day, evening or night hours, or full off-shift hours.
Expected to be on feet for 10 to 12 hours a day.
Climb upwards of 8 flights of stairs a day to maneuver within the manufacturing facility.
Lift up to 50 lbs, Carry 50 lbs, Push/Pull force of 50lbs with full body, and Push/Pull force of 24lbs with arms only may be required.
Ability to bend and lift items from floor level, work with arm extended at chest height while making fine hand and finger manipulations, extend arms above shoulder level to manipulate equipment, and repetitive fine motor skills.
Environment requires that gowning in the form of hospital scrubs, bunny suits, gloves and steel toe boots be worn.
No makeup or jewelry can be worn when working in the clean room environment.
Work in clean room environment with large mechanical equipment, piping, and pumps connecting to tanks serviced by high-pressure steam, water and air together this creates a loud environment.
Work with hazardous materials and chemicals.