Instrumentation Engineering Manager
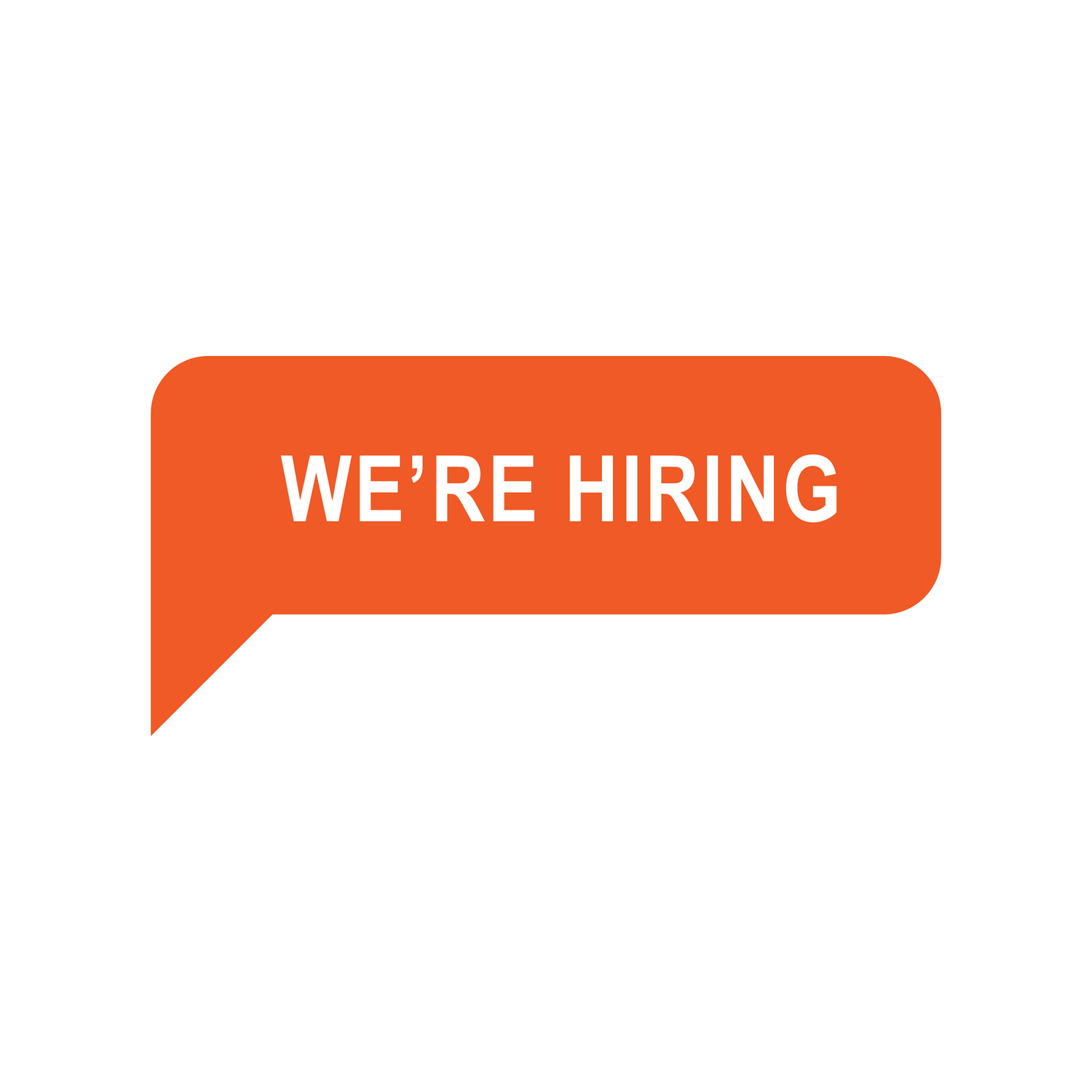
Envases
2021-12-03 19:00:02
Waco,
Texas,
United States
Job type: fulltime
Job industry: Engineering
Job description
ABOUT THE ORGANIZATION: The Envases Group is a worldwide supplier of quality packaging solutions. The Envases Group is divided into three packaging divisions - PET Packaging, Aluminum Beverage Packaging and Food & Industrial Packaging - each with special competences within their field to serve customers the best way possible.
Our core value is to supply high quality packaging solutions, always striving for growing our business in order to be the market leader in the markets we operate in.
Envases Group is expanding global presence by the plan to open its first aluminum beverage can production and distribution center in Waco, Texas. The Waco operation will focus on aluminum beverage containers commonly used for soft drinks, beers, energy drinks, teas and non-carbonated beverages.
Thank you for having interest in our employment opportunities.
REQ NUMBER: ENG-21-00012
CATEGORY: Engineering
EXEMPT/NON-EXEMPT: Exempt
FULL-TIME/PART-TIME: Full-Time
NUMBER OF OPENINGS: 1
SHIFT: Days
POSITION: Instrumentation Engineering Manager
Description
POSITION SUMMARY:
The Instrumentation & Electronic Engineering Manager provides technical support to projects from commissioning, startup and turnover to operations. This position requires a proven problem solver and equipment owner serving as a technical resource for the instrument and controls infrastructure support to projects. Ultimate responsibility for the efficient, safe, and reliable operating condition of the site manufacturing control and electrical systems is critical to our business success. In addition, it is expected that this individual will mentor and oversee a small team of maintenance E/I technicians, as well as work with the planner on preventative maintenance programs to enhance reliability. The Instrumentation & Electronic Engineering Manager must be a strong leader providing oversight to technicians to collectively be multi-skilled to manage, maintain, and troubleshoot site's electrical power systems, instrumentation, motor controls, PLC, HMI, data systems, and factory control infrastructure (servers, PC's, and networks). The selected candidate will be skilled in the design, installation, and upkeep of PLC based controls in a manufacturing environment.
ESSENTIAL JOB FUNCTIONS:
- Provide engineering expertise in the areas of test and integration of all machine installations, upgrades, ground support and production support of all the equipment and operating systems within the manufacturing facility; ensure power up and functional verification are optimal and sustainable for production volume requirements
- Lead the engineering and instrumentation technicians in support of the design, operation, material/component selection and procurement, construction, activation, and maintenance of data acquisition and control systems
- Provide support during machine installations and upgrades including: interfacing auxiliary equipment, identifying and correcting errors in programming and wiring and ensuring vendors and contractors are meeting our needs and expectations
- Utilizing Life Cycle Cost and Decision & Risk Analysis processes to assist with repair vs. replace decisions and infrastructure project needs
- Manage the design and installation of electrical/electronic equipment including electrical power distribution systems, PLC's, instrumentation, variable speed AC and DC drives
- Plan and perform work requiring a thorough knowledge of electrical/electronic and mechanical theories and principles. This includes writing specifications, local and national electrical codes, as they relate to a continuous operation process
- Partner with the maintenance planner to ensure electrical projects are properly scheduled on PMD's, and partner with the maintenance engineer to develop a good electrical/electronic preventative maintenance system
- Perform design calculations and prepare equipment or material specifications for electrical and electronic PLC based systems
- Periodically investigate and make an analysis of electrical or electronic based problems associated with the production operations, and take the appropriate action to correct these problems
- Maintain data acquisition systems
- Identify hardware requirements and compatibility
- Assemble, setup, and validate DAQ hardware configurations
- Troubleshoot DAQ hardware related problems
- Design wiring layouts and routing for interfacing to data acquisition systems
- Improve grounding and shielding of data systems
- Specify wiring specifications for harness builds
- Integration of new features into existing systems
- Provide technical support for instrumentation on all plant production machinery and operational equipment
- Provide and update drawings of electrical power systems, data/control systems
- Responsible for the creation and revision of I/O lists, Control System Narratives and Cause and Effect Diagrams, including range and settings management
- Provide troubleshooting support for electronic technicians
- Calibration of instrumentation sensors
- Evaluate new systems, technologies, and architectures to reduce development time, increase reliability and production line, and to streamline operations
- Support instrumentation technician with training materials, work tasks, and instrumentation documentation
- Review P&ID's to ensure correctness and consistency in the representation of instrumentation, control loops and control functions
- Develop, implement and maintain Personnel Warning systems
- Maintain inventory of instrumentation and control system hardware, and test and calibration equipment
- Support production line by monitoring and reviewing critical issue tickets, responding in a timely fashion to troubleshoot and remedy electrical equipment
- Participate in the safety programs and/or committees; follow all site safety policies, company policies and procedures work safely and wear appropriate PPE
- Identify and recommend changes to improve plant performance utilizing existing or new control systems; make program modifications in PLC's logic, HMI's programs and servo controller logic to improve equipment performance
- Diagnoses mechanical and electrical problems using technical drawings (e.g., blueprints, electronic/mechanical schematics) and diagnostic tools (e.g. multi-meter, laptop)
- Support the scheduling and purchasing of all instrumentation and control systems for projects; support the purchase, tracking, and expediting, as necessary, of all required instrumentation in order to meet project deadlines, including relief valves, control valves, metering and analytical instrumentation
- Assist and train maintenance, production or other technicians as needed with technical or troubleshooting related matters
- Ability to work in a team environment, record data in a computer system, communicate with multiple departments, and complete work orders and preventative maintenance on equipment indoors and outdoors
- Participate in the safety programs and/or committees; follow all site safety policies, company policies and procedures work safely and wear appropriate PPE
- Effectively communicating and engaging with other functional groups at all levels from craft persons and operators to plant leadership
- Provides overall management of the Instrumentation & Electronics Technician teams ensuring overall safe performance of machining and personnel operations while sustaining quality of product and timely distribution
- Manage and lead the team, ensuring adequate staffing levels, managing holiday allowances, recruitment, training, development, appraisal, attendance, disciplinary issues and daily supervision to maximize efficient productivity
- Motivate and coach the team to operational success
- Assess employee performance; provide positive and constructive feedback; provide conflict resolution; complete annual performance review process; address performance issues with corrective actions in performance improvement plans or through disciplinary actions; monitor the completion of tasks and ensure good performance and record on appropriate systems
- Apply qualitative and quantitative methods to measure team effectiveness and performance
- Consistently promote high standards through personal example and roll out through the team so that each member of the team understands the standards and behaviors expected of them
- Review, implement and update company records e.g. training matrices, performance reviews, risk assessments
- Lead the team in new product and process introduction
- Provide scheduling details, any needed instructional guidance of job assignments, correct procedures and applicable techniques to perform specific skills; ensure accuracy and completion
- Required - Bachelor's Degree in Electrical Engineering, Instrumentation & Electronic Engineering/Mechanical Electrical Engineering or related field
- Minimum 5 years' experience serving as an engineer in a metalworking industry, industrial maintenance, manufacturing or food industry
- 2 years' experience serving in a leadership/management role, preferred
- Project management experience
- Demonstrated ability to manage a 24-hour / 7-day week continuous operation
- Minimum 5 years' experience in maintenance and repair of instrument systems..... click apply for full job details