Mechanic - Process Automation Technician
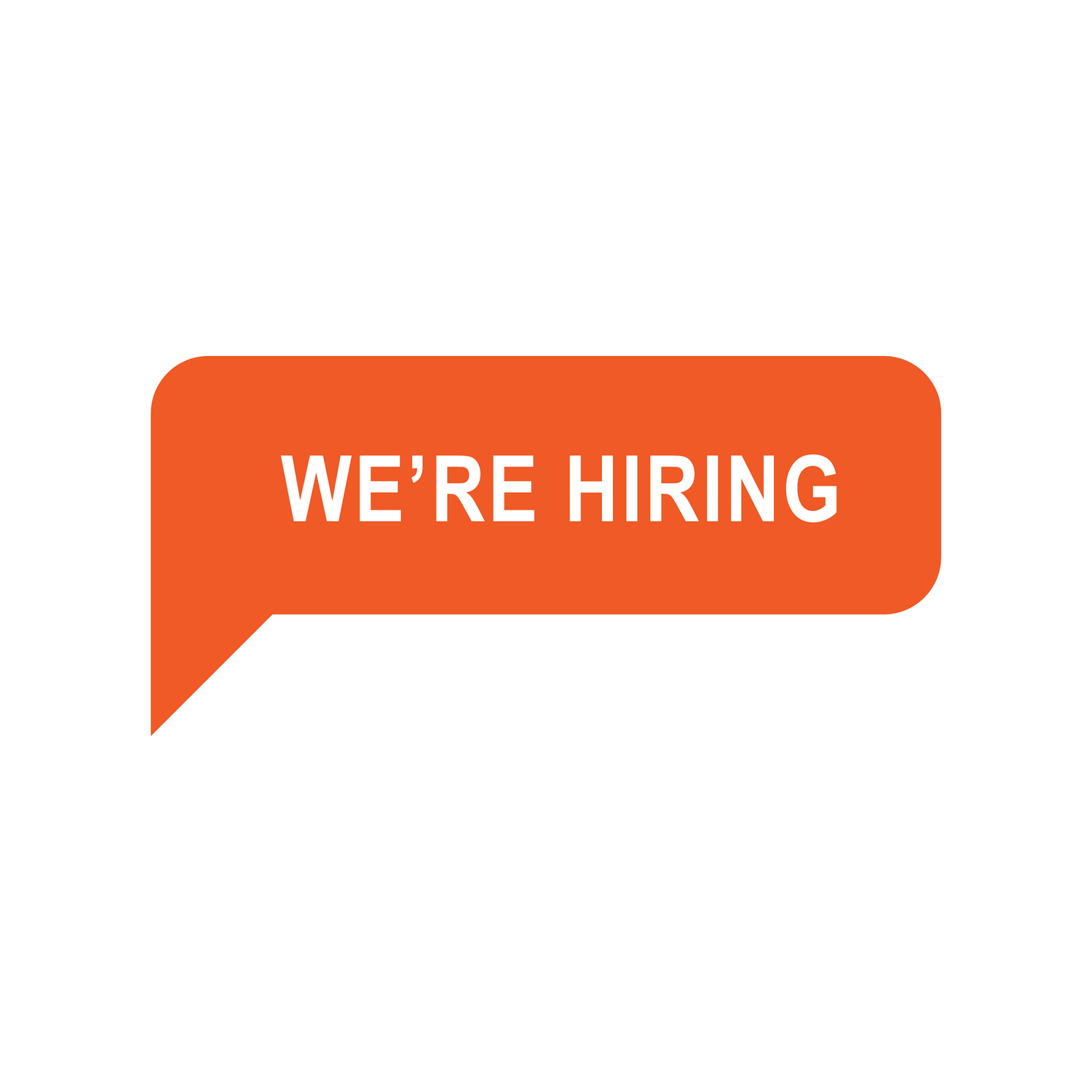
Ultralife
2021-12-03 09:02:09
Newark,
New York,
United States
Job type: fulltime
Job industry: Other
Job description
This role supports production as an automation technician of manufacturing operations. This position will particularly focus on automated production processes including computer-controlled systems and robotic devices (e.g. Allen Bradley hardware, RSLogix 500/5000 software, Scara robots.) The individual filling this role will install, setup, maintain, troubleshoot and repair equipment in support of the Company's quality and production standards. In addition, this role will incorporate responsibility for achievement of planned production goals in a safe, timely and cost-effective manner.
Essential Functions*: (Listing of specific duties in each area - in order of importance)
- Install, setup, maintain, troubleshoot and repair, mechanical, electrical, pneumatic, hydraulic and ultrasonic equipment.
- Perform routine diagnostic checks and monitoring of automated systems. Troubleshoot and repair automated systems, using knowledge of microprocessors, programmable controllers, electronics, circuit analysis, mechanics, sensors, feedback systems or pneumatics.
- Perform tasks such as preventive maintenance, line changeovers and equipment repair in a timely manner to avoid disruption to the production schedule.
- Manage and sustain the preventive maintenance activities using the Periodic Preventive Maintenance (PPM) database.
- Directly support development and installation of new production processes. Provide control system assistance during new or modified equipment startup.
- Create and update product drawings, fixturing, work instructions, test procedures and quality assurance requirements. Assist with any documentation updates to procedures or processes within work center.
- Validate or re-validate process and fixture capability.
- Participate in overall improvement activities leading to improved safety, enhanced efficiencies, better quality, and lower costs based on input obtained from cross functional sources including engineering, production and maintenance.
- Achieve production goals in accordance with scheduled build plans.
- Ensure work is executed to meet manufacturing quality standards and operational targets.
- Comply with and make recommendations to the Quality Management System.
- Promote lean initiatives related to products and processes.
- Adhere to all safety and policy regulations.
- Other assignments as deemed appropriate.
- Overtime as required.
Education / Training / Skills / Experience:
- Associates of Science; Engineering discipline preferred.
- Minimum of 5 years of experience in manufacturing environment(s) with demonstrated ability to fill an automated technician support role.
- Experience with installation, setup, maintenance, troubleshooting and repair of mechanical, electrical, pneumatic, hydraulic and ultrasonic equipment.
- Demonstrated knowledge of microprocessors, programmable controllers, electronics, circuit analysis, mechanics, sensors, feedback systems or pneumatics. Experience with Allen-Bradley hardware, Rockwell RS Logix software, Scara robots preferred. Previous work with Panasonic and Telemecanique will also be beneficial.
- Ability to read mechanical and electrical blueprints and have a solid understanding of basic electrical mechanical control systems to effectively learn and run automated systems.
- Strong math, computer and electronics skills; ability to work with hand tools and various instruments.
- Ability to identify and incorporate process and product improvements as well as adapt processes as needed for local manufacturing capability.
- Ability to work independently and interact with all organizational levels in a proactive, diligent and organized manner, with strong attention to detail.
- Excellent organizational, interpersonal and communication skills.
- High level of initiative and strong work ethic.
- Must have a general knowledge of ISO requirements and working knowledge of those requirements as they pertain to document / record control, new product development, identification / traceability / preservation of product, property management, supplier maintenance, monitoring / measuring / inspection / validation of product, control of nonconforming product, and corrective and preventive action in support of product manufacture.
Physical Requirements:
While performing the duties of this job the employee is occasionally required to stand; walk; sit; use hands to finger, handle, feel objects, tools or controls; reach with hands and arms; climb stairs; balance; stoop, kneel, crouch or crawl; speak and hear. The employee must be able to speak, read and write fluently, in English. The employee must occasionally lift and/or move up to 30 pounds. Specific vision abilities required by the job include close vision, distance vision, color vision, peripheral vision, depth perception and the ability to adjust focus.
*Employees must be able to perform the essential functions of the job with or without reasonable accommodation.
This job description is intended to convey information essential to understanding the scope of the position described above and it is not intended to be an exhaustive list of skills, efforts, duties, responsibilities or working conditions associated with the position.
Ultralife Corporation is an Equal Opportunity Employer, and as such affirms the right of every person to participate in all aspects of employment without regard to race, color, religion, sexual orientation, gender identity, national origin, citizenship, sex, age, veteran status, disability, genetic information, or any other protected characteristic. If you are interested in applying for employment and need special assistance or an accommodation to apply for a posted position, contact our Human Resources department via phone at 315- .
PI